Robotics/Types of Robots/Arms
Arms are types of jointed robot manipulator that allow robots to interact with their environment. Many have onboard controllers or translators to simplify communication, though they may be controlled directly or in any number of ways. Due to this fact, standalone arms are often classified as full robots.
There are many different types of robotic arms, but most can be characterized into one of six major categories by their mechanical structure. Cartesian (also known as Gantry) robots have three joints that are coincident with the standard X-Y-Z Cartesian axes. Cylindrical arms have any number of joints that operate on a cylindrical axis, normally rotating about one fixed rod. Spherical (polar) arms are those with joints that allow it full rotation throughout a spherical range. SCARA robots have two parallel rotary joints to allow full movement throughout a plane, typically for pick-and-place work. Articulated robots are used for complex assembly operations, and consist of three or more rotary joints. Parallel robots have three concurrent prismatic or rotary joints, and allow for tilting of heavy or sensitive platforms.

Robotic arms are typically used in industry. Repetitive autonomous robots perform one task repeatedly based upon predetermined movements and specifically located objects. Start and stop commands are determined by position, acceleration, deceleration, distance, and direction. More complex actions are executed based upon sensor processing. If object orientation or position is unknown, arms are often paired with machine vision and artificial intelligence to identify the object and subsequently control the arm.
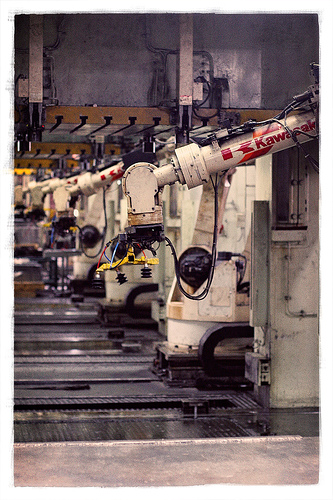
Arms are typically defined by fourteen different parameters.
Number of Axes – Two axes are needed to reach any point in a plane. Three are required to reach a point in space. Roll, pitch, and yaw control are required for full control of the end manipulator.
Degrees of Freedom – Number of points a robot can be directionally controlled around. A human arm has seven degrees; articulated arms typically have up to 6.
Working Envelope – Region of space a robot can encompass.
Working Space – The region in space a robot can fully interact with.
Kinematics – Arrangement and types of joints (Cartesian, Cylindrical, Spherical, SCARA, Articulated, Parallel)
Payload – Amount that can be lifted and carried
Speed – May be defined by individual or total angular or linear movement speed
Acceleration – Limits maximum speed over short distances. Acceleration is given in terms of each degree of freedom or by axis.
Accuracy – Given as a best case with modifiers based upon movement speed and position from optimal within the envelope.
Repeatability – More closely related to precision than accuracy. Robots with a low repeatability factor and high accuracy often need only to be recalibrated.
Motion Control – For certain applications, arms may only need to move to certain points in the working space. They may also need to interact with all possible points.
Power Source – Electric motors or hydraulics are typically used, though new methods are emerging and being tested.
Drive – Motors may be hooked directly to segments for direct drive. They may also be attached via gears or in a harmonic drive system
Compliance – Measure of the distance or angle a robot joint will move under a force.
The arm itself is only responsible for positioning. An end effector is necessary for actual environmental interaction. Some common choices are grippers, sprayers, grinders, welders, and vacuums, though many other options are available. There is a large variance in complexity, ranging from flush mounted, non-moving parts (magnets or sticky pads) to multi-jointed, multi-sensor parts with various inputs and outputs. End effectors are typically chosen based upon the application, and many arms will fit multiple end effectors.
A 2006 Japanese report shows that 60% of robotic arm installations were for articulated robots, 22% were for gantry, 13% were SCARA, and 4% were Cylindrical. The automobile industry has the highest concentration of industrial robots with nearly 1 robot per 10 people.
Biological design of robotic components is becoming increasingly popular. Currently, the Shadow Company (famous for the Shadow Hand) is working on a biomorphic arm that accurately models a human arm. The arm has seven degrees of freedom like the human arm which greatly increases its efficiency.

Researchers at Fraunhofer Institute for Manufacturing Engineering and Automation IPA in Stuttgart have begun working on an arm that is modeled after an elephant’s trunk. The arm uses a cord that is connected to a drive shaft at its midpoint. When the shaft turns, the cord wraps around it both ways forming a double helix. Their prototype arm uses ten of these cord systems with two motors attached to each (the second acts as a failsafe for increased safety).
Similarly, biologists at Hebrew University in Jerusalem are studying Octopi tentacles as a possible model for future robotic arm development. An prototype has not yet been built, but arm design has recently begun.
Additionally, two monkeys learned to control robotic arms through sensors implanted on their brains in a study performed the University of Pittsburgh and Carnegie Mellon University. While not currently practical, the study confirms that brain-controlled prosthetics are feasible and has sparked interest in the area.