The Seed Factory Project
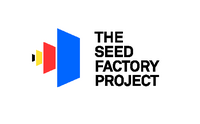
- 1.0 - Project Organization
NOTE: some section numbers on this and the following pages are missing because we have not created any content for them yet. We are using a complete outline to number the existing sections to avoid having to renumber them later.
1.1 - Project Structure
[edit | edit source]
1.1.0 - Structure Design
[edit | edit source]
Introduction
This project started with one person pursuing an idea. Like many engineering projects, seed factories are too complicated for one person to design and build, and they require more resources than the average person has available. If multiple people are involved, their work should be coordinated, so that it can be carried out efficiently and reach technically sound results. So the project should have some structure and methods to do the coordination. They should derive from what the project is doing and wants to do in the future. We expect the project's needs to evolve over time, as the number of people, costs, and returns increase. Therefore we plan for the structure and methods to also evolve.
Evolution Concept
Open collaborations have been very successful in software development, and more recently are starting to be used for hardware projects. So we decided to follow that route to start with. "We" refers to all the people who have contributed in some way to the project. Early stages of design can mostly be carried out on computers, and most people capable of doing that work already have them. So funding sources and compensation are not required for these stages. The return for early efforts will be open-source designs and technology that anyone can use. Contributors would benefit themselves by gaining access to other contributor's work. For some people, contributing to the good of society or gaining personal experience and skills are sufficient rewards. Since the design is intended to be open-sourced, it is open for any competent contributor. If people contribute their work, we request they include data sources and calculations, so that others can check and improve on it.
When the project moves on to building workshops and equipment, costs will increase to significant levels, so the project structure needs to change. We expect to become a distributed project with multiple physical locations, since the interested people won't all be in one place. Project members will own the specific sites and hardware they contribute to, and benefit from any products they produce. The designs and technology will remain open-sourced for anyone to use. The intent is for members to get proportional ownership according to what they put into the project. Inputs can be design work, funding, tools, materials, and physical labor. An example organization at this stage is a network of individuals, small partnerships, and community cooperatives who help each other make things. Aside from personal satisfaction, the reward at this stage is the ability to make things for hobby and home use for themselves or for their local community.
As the designs and prototypes become better developed, some people may move on to commercial enterprises. So long as production output is not sold, it is not business income, so informal associations are sufficient. Once people begin selling things on a regular basis, the legal and tax requirements change, and formal business organizations would need to be set up. The exact legal structure will need expert input and need to follow local laws. Most likely, the commercial entities will need to be spun out of the original project, so that it can remain open-source and not-for-profit. An example commercial structure is a limited liability corporation (LLC). Commercial entities can interact with open source efforts by selling products, giving design feedback, and requesting new designs to serve commercial needs.
Coordination Tasks
We use the term "project coordination" rather than Project Management because the project as a whole does not use a traditional top-down command structure. We may use some traditional management tools, but we have to account for people contributing their efforts on a voluntary basis. Therefore we cannot order people to do something because their paycheck depends on it. Rather, we request particular tasks be done, and who would be suited to do it, but people can choose tasks or not on their own initiative. Operating in this way requires being visible about project plans and status, which is why project information (such as this page) are in wiki format. Duplicate efforts are wasteful, so part of coordination is supplying tracking of who is doing what, so that people interested in the same tasks can communicate and share the work.
Based on systems engineering experience for complex projects, we have identified the following sub-tasks within the overall coordination effort:
- Coordinate External Flows - includes arranging and managing resource flows into and out of the project, to and from the larger program of which it is part, other projects, or society as a whole.
- Coordinate Tasking - includes arranging which resources will be applied to particular project tasks.
- Coordinate Planning & Scheduling - includes developing future plans and schedules for the project.
- Coordinate Analyses - examines past performance and studies ways to improve project processes.
1.2 - Project Resources
[edit | edit source]Sufficient resources are needed to keep the project moving forward. In the early stages they include people with time and necessary skills, data sources, general workshops and custom facilities, and general computing, communications, and working spaces like offices. Computer-based design, simulation, and software development is much cheaper, aside from the human time involved, than building hardware. So we will try to do as much of the early work as possible electronically. As it becomes necessary to prove a new component technology, or as element design is sufficiently complete, we will transition to fabricating hardware. The partially-built workshops and facilities can be used immediately to make items for the project members or for outside sale. So they can be useful and productive as soon as enough is working, and help bootstrap later work.
Full identification of all needed resources will be the result of treating the project as a system to be engineered. Resources then become inputs to project tasks, which in turn produce intermediate or final project outputs. This involves modeling and analysis of the project which has barely been started at this point. The following subsections identify what the project has on hand already and near-term plans as of September 2016. This will be updated as engineering of the project continues.
1.2.2 - Project Data Sources
[edit | edit source]
Any engineering project needs inputs of previously existing data. Existing data represents knowledge and experience gained from past work, and thus avoids having to re-learn or re-create things that already exist. Our current project data sources include:
- A paper technical library of about 400 books and magazines on science and technology topics.
- Paper technical files consisting of about 6 linear meters of file drawers and ring binders, mostly relating to space systems, supplied by the project's founder. This will be used for later project phase application of seed factories beyond Earth.
- A digital technical library of about 2500 science and technology documents, 26 GB in size, mainly PDF format books and articles.
We have access to the Internet, which of course is a vast repository of data on every imaginable subject. Of special interest are a number of government data repositories on relevant topics. Anyone can post information online, so care is needed to identify reliable data. This can be done by checking multiple sources, and considering the quality of the authorship, editing, and review that goes into a particular item.
In addition to online sources, we also expect to contact companies, institutions, and experts who have specialized knowledge, particularly in areas like manufacturing and industrial automation.
1.2.5 - Project Facilities
[edit | edit source]
Facilities are durable capital assets, such as land and buildings, which are available for use by the project. We can divide them into categories by ownership: owned by the project, leased by the project, and owned separately by individuals and groups but contribute use or access. Seed factories are designed to grow by making more equipment, and often grow in the other sense of living organic products, like trees that produce wood. They also can collect renewable energy and extract raw materials. All of this requires sufficient physical space in the form of land, and improvements like buildings and roads. In later generation designs, physical space can also include open waters and space beyond the Earth.
For now, the project has purchased 10,800 square meters (2.67 acres) of residential land near Atlanta, with about 185 square meters (2000 square feet) of indoor office and workshop space, and 93 square meters (1000 square feet) of covered outdoor space. The total built up and paved area of 345 square meters (3700 square feet) is only 3.2% of the property, so there is considerable room for growth. If the project outgrows this location, the Atlanta metro area has large amounts of industrial and undeveloped land, with a good amount near our current Fairburn, GA property. We also have a rented 14 sq meter (10x15 ft) storage unit full of tools and materials that will eventually go in the workshop.
Our current facilities are allocated as follows:
- Office - 1 room, 4 desks, 3 computers, 13 file drawers, 7 open shelves (functioning)
- Library - 1 room, 3 bookcases technical books
- Light crafts - 2 rooms: Sun Room (mostly empty, being prepped), Craft Room (mostly storage)
- Workshop - full basement, bare slab and block walls. Temporary work space set up, but needs renovation work (painting, electrical, lighting, etc.) for permanent shop.
- Covered space - currently vehicle parking and outside storage (may be enclosed later and upgraded to working space)
- Open land - 80% wooded/20% grass. The trees are a future lumber supply, and the open land in general is for future expansion. We don't expect to convert more than 10-15% of the land area to indoor space, due to zoning rules, paved areas, energy collection, materials extraction, and continuing to grow trees and other plants.
1.3 - Project Planning
[edit | edit source]Plans describe how we expect to carry out the project work. It includes internal planning of the organization and structure of the project, and technical planning for the designs and prototypes that are the project's objective. Project plans are currently in an early state, and the following notes are to be incorporated into them as they get more developed.
Planning Notes
1. - As an open collaboration, we can't tell anyone what to work on. But compared to software, hardware takes more money for equipment and materials. It makes sense to do more of the design work first, so that the hardware won't require as much trial and error later. It also makes sense to apply Systems Engineering methods, which were developed to coordinate complex projects. Most people with the right design skills already have access to suitable computers and basic software. Computer-based design, simulation and software development are much less expensive in terms of equipment than physical hardware. So the early stages of the project doesn't need much outside funding. That will change once hardware work begins, and you need physical work space, equipment, and materials. Also, as we get deeper into the work, we may not find qualified people willing to contribute their efforts, and have to hire specialists.
2. - We will not have project cost estimates until concept exploration is done and we know what component technologies and prototypes need to be built. Small-scale prototypes for hobby and home use will not be very expensive. Building a large-scale set of equipment that supports the needs of a community is on the scale of industrial and real estate development. That would require significant amounts of funding, but there are also conventional ways to supply such funding. By that time we should have demonstrated operating prototypes, which should make funding easier. We should also be able to bootstrap some of our own construction and equipment needs.
3. - For the physical aspect of the project, we expect there to be one or more locations where the prototype hardware is assembled and tested. So whatever hands-on labor is required will need to use people from the local region, or members who can travel there. If there is enough interest and it makes sense, individuals and satellite groups can work elsewhere and ship parts and hardware to a main location for assembly. In return, outputs from the finished equipment will be delivered directly to local members, or shipped if they are further away.
4. - The equipment is intended to be flexible and programmable, and can therefore make a wide variety of items. Project members will be able to submit design files or select previously designed items to be made to order, according to their proportional share in the project. Members should be able to mark design files as private (for their own use only), or public (contributed to a library for anyone to use or modify). Submitting designs or production orders would be similar to rapid prototyping/3D printing services or conventional fabrication shops, except that project members also own the equipment. So they are using their own equipment to make things for themselves. The project can also accept orders from the general public and sell surplus production to help pay for things we cannot make internally.
5. - A design goal for project Phase 2A, distributed small business and commercial scale production, is to support most of the food, housing, and utility needs of the owners and local community. So once a network of equipment is operating and growing, they can start to buy and develop local real estate. The network would produce building materials, grow food, generate power and supply clean water. Members can then build residences, office buildings, and other items for themselves or to lease to others. Because their equipment starts from common raw materials and uses automation, these end products may be much less expensive than conventional versions. If the first location is successful, then new seed factories can be set up in other locations and the whole process replicated. This kind of commercial development would be spun out of the Seed Factory Project, but use their designs.
1.3.1 - Internal Project Planning
[edit | edit source]
1.3.1.1 - Systems Engineering Planning
[edit | edit source]
The systems engineering approach considers the whole life cycle, from early concepts to final disposal (Figure 1.3-1). In this way, total cost, resource needs, and waste products can be accounted for. The life cycle is divided into a sequence of stages, such as concept exploration, preliminary and detailed design, fabrication, test, installation, operation, maintenance, and decommissioning. The useful benefits of a system come during operations, but the other stages are needed to get to them. We want to apply the seed factory concept to different locations with different end purposes and environments. That will require specific designs for each. So the project is divided into phases, generally going from easy to harder as we gain experience (see section 1.3.2 below). Each phase follows the life cycle pattern, with shared research and development going on before and in parallel with the early parts of successive phases.
- Concept Exploration Stage
Concept exploration is the first stage of the project. It starts with unmet needs and desires that cause people to look for ways of satisfying them. The result of this stage is one or more "system concepts" that can meet the goals within constraints like time, funding, and technical feasibility. A thorough job looks at all possible approaches to meeting the goals, narrows them down to the best solutions, and estimates if it can be done within the set limits. A choice then is made to proceed to further design stages, abandon the project, pursue R&D in areas that need improvement, or wait for better conditions and ideas. Concept exploration requires people with appropriate skills, and computers with appropriate software. It does not require much other hardware, since physical construction and testing happen in later stages.
We did an early Concept Exploration Study in 2013, that encouraged us to go further. The notes are attached to the Seed Factories wikibook. The study is incomplete, but you can refer to it if you want to see the prior work. The study treated a factory and the community it supports as an interrelated system with input and output flows between them and with the outside world. We then used the basic engineering principle that matter and energy are conserved, in other words they do not appear or vanish from nothing. So all resource flows of whatever type that enter and leave the system, or move between it's parts, must be accounted for in a complete design. This includes raw materials, recycled items, and final waste outputs. Design goals for sustainability were to use up more waste in the form of trash and scrap inputs from outside sources than we create, and to leave the land in better condition than it started. We don't know yet if those goals can be reached. By explicitly considering all the resource flows we will at least know where we stand relative to the goals, and what items need improving to reach them.
That study was a point design for a single set of outputs at a particular scale. Our current work considers a growth sequence that starts with hobby and home use, which is smaller and simpler than meeting a majority of community needs. It then would grow past the community level to industrial scale and more advanced applications. We will incorporate the prior work as appropriate. The actual design process mostly works backwards from the industrial scale to the smallest starter set. That approach ensures the entire growth sequence is workable. Designing mostly in the forward direction, from small to large, is more likely to find unexpected items on the path. This then forces redesign of the earlier phases to include them.
The first self-bootstrapping equipment and processes that make up a seed factory must be built using existing conventional tools and equipment. So part of the design process works forward from what is already available. For example, an advanced seed factory may use robots to assemble extensions to the factory building it uses. But for the first such building, those robots are not yet available, so it would be built by conventional construction methods. Parts for the first robots would be made with conventional machine tools, and so on. The people who will build and operate a seed factory do not start out knowing how to do it, because nobody has the required experience yet. So we must start with the skills and knowledge people already have. Then we can work forward to build what they already know how to build, and what added skills and knowledge they need for later. The combination of working backwards from desired end points, and working forwards from existing experience and equipment, should result in a feasible project path.
- Later Design and Development Stages
If a good enough result comes from concept exploration, a decision to continue the project is made. Enough resources must then be gathered for further design and development. This includes design, new technology development, and hardware demonstrations. Design typically goes through a couple of stages. Preliminary design takes one or more system concepts, identifies the main elements of hardware, software, facilities, etc., and determines overall dimensions, layout, weights, and subsystems. For example, a lathe may have subsystems for manual and automated controls, drive motor, and structural frame. Detailed design takes the preliminary design to the point that all the parts can be manufactured or ordered, software is specified to a detailed level, facilities are ready to begin construction, and so on.
- Research and Development
Concept exploration may point to new technologies or processes that are worth investing research and development (R&D) resources into. The current state of the art in a given field has no risk associated with it. It is a known quantity, and design can proceed right away with reasonable certainty of the result. R&D is inherently risky, because after doing the work, you may not get a useful result. So you have to do a risk vs. potential gain evaluation and decide if it is worth it. The timing of the R&D depends on when you need it. If your system concept won't work at all without a given technology, the R&D must come first. If you only need it for a later project phase, you can wait to start that R&D till later. A happy side-effect of doing difficult things like R&D is people can come up with alternate uses or unanticipated ideas. You cannot schedule these events, but you can plan ahead for what to do when they occur.
Part of R&D involves building prototype components and machines, so you can test the technology or process, measure efficiency, etc. This may be done multiple times until it is good enough, or abandoned. The knowledge from measurements and tests can then be applied to the design of final production systems.
- Later Stages
As design and R&D are completed for pieces of equipment, they can move on to the later life-cycle stages:
- Fabrication - making the parts and bulk materials like fluids used in the equipment.
- Assembly - combining the parts and materials into finished equipment.
- Test - more extensive component and functional element tests for the first few units, basic tests for later production.
- Verification - proving the finished equipment does what it was intended to do, by means of inspection, demonstration, system test, and analysis.
- Installation - delivery, set up, and connecting to utilities and other equipment for fixed location items.
- Deployment - delivery of vehicles and mobile equipment to operating locations.
- Operation - using the equipment productively for the intended purpose, which is the reason all the other stages happen.
- Maintenance - tasks like cleaning, lubrication, and replacing worn or broken parts, in order to keep the equipment working, and finally
- Decommission - disassembly, removal, and recycling of equipment that has reached the end of its useful life.
All the life cycle stages are not a strict linear sequence. Later stages impose needs on the earlier design process. For example, assembly requires sufficient physical space, assembly tools, a design that permits access as the various parts are put together, and instructions for the assembly sequence. Experience from later stages, like operations and maintenance, can feed back to the design stages for corrections and upgrades to later versions. So the systems engineering process as a whole involves the entire life cycle from start to finish, but has many cycles and feedback loops within the process.
1.3.2 - General Technical Planning
[edit | edit source]
1.3.2.1 - Project Phases
[edit | edit source]

The project itself, as distinct from the equipment and end products we are building, is complex. So we can recursively apply systems engineering methods to planning the technical work. One method is division of a complex project into smaller and simpler pieces which are easier to work on. In our case we can divide the project by life cycle stage and project phase. Each piece is then treated as a functional task, with connecting flows to and from other tasks and outside the project. The life cycle stages were listed in section 1.3.1.1 and are fairly standard for large engineering projects.
Project phases derive from the idea that seed factories will not all be the same. Over time we will acquire more experience with building and operating them, and we expect technology in general to improve, in addition to the R&D work we do ourselves. Particular locations will have different desired production outputs and operating environments. One output choice is a given location making new starter sets for new locations. All of these differences lead to different design choices for the facilities and equipment.
This led us to identify a sequence of seven major project phases and sixteen sub-phases to cover the range of possible project designs (Figure 1.3-2). The sequence generally goes from easier to harder and from nearby to distant. The connecting arrows indicate which phases can support a later one by supplying outputs and resources for them. After starter sets (seeds) have grown to full production capacity at a given location, they have an indefinite operating life. They would be maintained and upgraded as needed, and operate for as long as people want what they make. So project phases don't end, instead they build on each other and continue in parallel. This is similar to how large real estate projects are often carried out. They have a sequence of construction phases, but what's built in each phase continues to be used while later phases are built.
The major phases are numbered from zero to six and named as follows. Sub-phases are numbered with an additional letter after the major phase number, and are displayed in the figure:
- 0 - Research and Development
- 1 - Starter Locations and Network
- 2 - Moderate Locations
- 3 - Other Earth Locations
- 4 - Orbital Locations
- 5 - Planetary System Locations
- 6 - Interstellar Locations
Phase 0 - Research and Development (R&D) comes first because some R&D is needed before the first starter locations can be built. R&D continues as needed to support later location types. Each phase and sub-phase can include many individual locations, but these locations will be similar to each other in terms of local environmental conditions. So the equipment designs can be shared across the group of locations. This is similar to how automobiles can be used in many locations without changes, but if they are used in arctic or desert conditions, they may need some changes to work properly.
The project's initiator is a space systems engineer, and the seed factory concept started out as a way to enable future space projects that would otherwise be too difficult and expensive. Phases 4 through 6 cover these types of locations. However, despite personal interest, there are more immediate needs and applications on Earth. Building such systems on Earth will also accumulate experience for the later and more difficult locations. Phase 3 covers difficult and extreme environments on Earth, such as deserts, ice caps, and the oceans. Few people currently live and work in these environments, and setting up production locations would be harder than in more moderate conditions. Therefore most of our early effort will be concentrated on Phases 0 to 2. These all begin in moderate environments with nearby populations, and access to infrastructure like roads and utilities. Therefore they are the easiest locations to build first. As they are built up, their production outputs plus accumulated experience allows going to the more difficult locations in the later phases.
1.3.2.2 - Phase 0 - R&D: General Planning
[edit | edit source]
Throughout history, tools have always been used to make more tools, in addition to finished items that people use. There are already many existing tools, machines, and processes that can be used to make things. What's new and different about seed factories, that would need additional research and development includes:
- The the equipment is designed to work together and grow from a small starter set.
- The growth follows planned sequences using stored files and instructions.
- Increasing levels of automation and self-production are used as capacity grows.
- The expanded factory can eventually produce new starter sets.
Existing conventional tools and equipment are needed in order to build the first starter set items. So part of the R&D effort is how to start with the conventional items, transition to partial and full starter sets, and then move to increasing automation and self-production. We don't expect to design everything at once, or to get it perfect the first time. So another part of the R&D task is to figure out what to work on first, based on the growth sequences, best return on effort, and useful end-products that can be made. It has to be kept in mind that growth for its own sake isn't the point of a self-expanding factory. Rather, it is just a more efficient way to get the things people need and want.
Some designs, or parts thereof, can be built with current technology. If not, and sufficient work is being done outside the project, or the potential gains from the new technology are small relative to the effort, we may decide not to devote our efforts to a given area. If there is a lack of work by others, and significant gains are possible, we can choose put effort into research and development of new technologies. Note there is no guarantee the effort will succeed. Skills and experience in the relevant fields will improve the chances of good results, so it is important to find the right people, or build their knowledge. But the nature of working on new technology is that sometimes you get no results. That possibility should be accepted, and backup plans in place in case it doesn't.
The general R&D process steps include:
- Identify the technology categories needed for a given project phase and stage
- Survey the existing state of the art in these categories
- Identify any deficiencies in knowledge or performance needed for these technologies
- Provide analysis tools, lab and workshop space, staff etc. to address these deficiencies
- Develop and test component-level improvements
- Integrate, build, and test functional prototypes with these improvements
- Document and disseminate the results of the new technology work
- Sub-phases for Phase 0 - R&D
The R&D phase can be also be subdivided into smaller pieces in order to make planning and executing the work easier. The obvious way to do this is according to which later phase the R&D is targeted for. We also can have R&D that applies across multiple phases or the whole project. Cross-project R&D gets no specific number. That work is collected under the main Phase 0 heading. Sub-phases are numbered 0A to 0S according to the later project phases and sub-phases the work is targeted to. If work applies to several areas, it is numbered with all the corresponding letters, such as 0CD or 0G-L. The sub-phases are:
- 0A - R&D For Phase 0 R&D Locations
- 0B - R&D For Phase 1 Starter & Network Locations
- 0C - R&D For Phase 2A Distributed Locations
- 0D - R&D For Phase 2B Industrial Locations
- 0E - R&D For Phase 3A Difficult Earth Locations
- 0F - R&D For Phase 3B Extreme Earth Locations
- 0G - R&D For Phase 4A Low Orbit Locations
- 0H - R&D For Phase 4B High Orbit Locations
- 0I - R&D For Phase 4C Inner Interplanetary Locations
- 0J - R&D For Phase 4D Main Belt & Trojan Locations
- 0K - R&D For Phase 4E Outer Interplanetary Locations
- 0L - R&D For Phase 4F Scattered, Hills & Oort Locations
- 0M - R&D For Phase 5A Lunar Locations
- 0N - R&D For Phase 5B Mars Locations
- 0O - R&D For Phase 5C Venus & Mercury Locations
- 0P - R&D For Phase 5D Jupiter System Locations
- 0Q - R&D For Phase 5E Outer Gas Giant Locations
- 0R - R&D For Phase 6A Interstellar Space Locations
- 0S - R&D For Phase 6B Exostellar Locations
- R&D Process for Phase 0A R&D Locations
The R&D locations used in Phase 0 may themselves require some new technology or other research to build. However we expect most of the R&D locations to consist of conventional facilities and equipment. This is because science and engineering are well developed fields, and there is already a lot of accumulated experience in building those kinds of places to do the work. R&D locations will include offices, laboratories, workshops, production, test, and storage areas. These locations must be designed too, in addition to the equipment, factories, and locations that are the point of the project. A general process for R&D location design includes:
- Flow down objectives and requirements for the R&D locations from overall project goals and larger civilization needs. Also flow back needs from later project phases. For example, if industrial scale machines are needed in Phase 2B, then the R&D spaces must be large and sturdy enough to assemble and test these machines.
- Analyze the internal functional tasks of the R&D locations, and the flows among the tasks and among outside entities.
- Design location options to meet the requirements and perform the tasks identified.
- Trade off alternative options and optimize technical parameters according to chosen evaluation measures
- Document a baseline for the next cycle of design, or a final design to proceed to construction.
1.3.2.3 - Phase 1 - General Planning
[edit | edit source]
1.3.3 - Specialty Technical Planning
[edit | edit source]
A number of engineering specialties are typically involved in a large and complex project. Examples are software development, factory maintenance, and safety/risk management. These may each need plans for how they carry out their work, and how their work connects to what other people are doing. This section will cover the planning for the various specialties.
1.4 - Project Tasking
[edit | edit source]Tasking includes defining, selecting, and assigning technical tasks to the people who will perform them. At this stage of the project, concept exploration, that means self-selected volunteers choose which parts to work on at their own pace. This section will note which tasks need to be done, and which people or teams have taken them on.
1.5 - Project Documentation
[edit | edit source]Project documentation refers to how the project works internally, as distinct from the engineered products we intend to produce.
1.5.0 - Project Models
[edit | edit source]A model in the engineering sense is a simplified version of a more complex system, used to analyze, understand, and present it. Architects, for example, can build physical scale models of a project to understand the relationship to surrounding buildings, lighting, floor plans, etc. System models are more commonly abstract, digital, and mathematical representations because a complex system isn't a rigid 3-dimensional relationship of its parts the way a building is.
1.5.0.1 - Project Operating Model
[edit | edit source]
A business model is an abstract explanation of how the members of a business project get rewarded for their efforts. This is usually in terms of money, because money in a capitalist system can be traded for most other goods. However, in our case, project members can contribute voluntarily, and also make products they use themselves, without having to trade for them further. So we refer to this activity as an Operating Model instead.
Project Goals and Objectives
The project should be designed to support and complete the goals and objectives we set for it. In turn, the goals and objectives come from needs identified in the larger program to upgrade civilization.
- Project Goals
- Provide the most benefit for the most people.
- Provide a fair return to project members for their efforts. These returns may be other than economic ones.
- Contribute to financial independence and security against job loss.
- Contribute to program-level upgrades to civilization and solving its existing problems.
- Project Objectives
The main objective of the Seed Factory Project is to provide designs and working prototypes of self-bootstrapping automated production equipment. A starter set of equipment is called a Seed Factory, in the sense a plant seed can grow. Like any factory, it produces useful end-products. But it also makes parts and materials for more equipment to expand itself. These can either be copies of the starter set equipment, different sizes (usually larger), or entirely new items not in the starter set. The automated equipment follows stored design instructions for both end-products and self-expansion, but the factory is not fully automated. Some people are needed, especially at first, to perform manual tasks, operate the equipment, and assemble finished items. Factory growth is open-ended and can grow to any desired size and complexity. Eventually new starter sets can be produced to repeat the growth process in new locations. Specific objectives include:
- Improve the ratio of working to non-working assets, and increase the efficiency of working assets. Non-working assets are items like parts and materials which sit on a shelf, while working assets are items like robots and machine tools actively performing tasks.
Project Description
The Seed Factory Project itself is organized as an open-source non-profit activity. It performs the R&D, design and prototyping for self-expanding production systems, and relies at first on volunteer efforts and contributions to operate. Once useful methods and hardware are developed, they can be spun off as gainful activities and businesses. These can later support further work by the Project, because they will get improved and upgraded equipment and processes in return. Outside support may be financial, or by assigning staff or part of their own production. The Project and spun-off enterprises will evolve in phases of increasing size and complexity, so we will discuss the project model in those terms.
While project designs are open-sourced, people will own any spun-off physical equipment and outputs they make. These can be full ownership of individual items, or a share in a larger collection like a workshop or factory. The ownership arrangements would be a matter of choice and agreement among the members. This approach is intended to satisfy the dual goals of a fair return for people's efforts, and the most benefits to society at large by making use of the designs unrestricted.
As individuals, people can have various personal goals and reasons for participating. These include financial independence by owning their own business or productive assets, security against job loss by supplying their own basic needs, and contributing to the general welfare of society by upgrading development and solving pressing problems.
Project Path
In section 1.3.2 - Technical Planning we identify seven major project phases. The first three of those are Phase 0 - Research and Development (R&D), Phase 1 - Starter Locations and Network, and Phase 2 - Moderate Locations. R&D provides the necessary research, design, and prototyping for the later phases. Phases 1 and 2 develop production locations in moderate climates on Earth. These are the easiest conditions to design and build for, and therefore come before more difficult and remote places in later phases. The two phases differ in scale and product range, going from smaller and simpler to larger and more complex. Each phase builds on the experience gained in the previous ones. The R&D phase builds on existing industrial technology and engineering experience.
The first three phases will consume most of our early efforts, so we provide some more details how we expect them to operate. The project itself is subject to internal design, in addition to the production equipment we want to develop. So the following details are a starting point, and subject to change.
- Phase 0: Research and Development (R&D)
We assume that early project members don't have a lot of time or financial resources to contribute. So we begin as a distributed design effort, similar to how open-source software is developed. We use open format documents like this wiki, which people can work on as time permits. We expect to use engineering design software later on, once we reach detailed hardware planning. Because of the technical nature of the work, designers will need knowledge from the relevant fields, or learn as they go. We are unlikely to get all the needed experts just showing up in the various specialties, at least at first. We have two approaches to cover these gaps. The first is internal development of needed skills. The project can develop and point to tutorials and training for those who want it. An example is the Seed Factories wikibook. It is intended as an introductory textbook on the subjects of our project, though at present it is only a partial draft. The second is to develop interest and collaboration with existing experts. For example, robotics researchers may find seed factories an interesting application for their work, if we tell them about it, and we can then exchange information and advice.
As the design progresses towards prototype equipment, the cost and time demands will increase, and self-funding on a volunteer basis will reach its limits. To justify their efforts, project members will need to produce products and services for their own use, or look to more conventional venture and start-up funding. This would be based on the prototypes leading to marketable products. Another option is to solicit contributions and grants for further research on a charitable basis, or perform contract research for other organizations. Project members can then transition from volunteers to paid staff.
- Phase 1 - Starter Locations & Network
Network - As plans and designs make progress during R&D, we can start to develop a community of people and equipment who help each other make things. We call this a MakerNet. This would start with whatever skills and tools people already have, and begin a process of upgrading their skills and acquiring or building personal-scale production equipment. These are sized for hobby and home use products at first. They are mostly conventional items to start with, but increasingly use new designs developed by the Project's R&D.
The MakerNet starts out on a spare time/hobby basis. Many people don't have physical space or funds for a full workshop. So we assume they will (1) house one or a few equipment items each at home, (2) share larger fixed working spaces, or (3) bring mobile equipment to a temporary location as needed. Members who live within easy travel range make items for themselves and physically help make items for other members, based on their interests, skills, and equipment. Easy travel range, typically 0.5 to 2 hours in developed areas, is what defines a Location. That's because sometimes people and equipment have to be brought physically together to finish a project. Members who are beyond easy travel range can start their own locations with their own local production networks. People from different locations can trade software and digital designs, or ship items small enough and high enough value to be worth sending physically.
The network is designed to accommodate new members at whatever level they come in with. People who have no spare funds and no conventional tools can start by contributing their labor, as there are always tasks that need doing. Their labor can be traded for items they want, or accumulated as credits toward future equipment shares. If they lack the necessary skills, they can learn by doing, use educational materials, or get training from other members. People who have some spare funds but no tools yet can save up in high yield/leveraged conventional investments, according to their risk tolerance. The accumulated funds would be put towards later equipment. People who already have sufficient funds can directly buy into a share of materials, tools and equipment. People who already have hobby or commercial grade equipment and skills can immediately join the network and begin helping each other.
The network would use popular methods to coordinate: meetings and build events, email, phone, websites, etc. Members maintain shared lists of people, skills, equipment, and who is willing to do what to help each other. When better and less expensive automation and remote operation technology is obtained, more work can be done beyond a single location, and different local networks can link up and collaborate.
Starter Locations - As the R&D progresses, eventually complete sets of plans and instructions, and even ready-to-use equipment, can be provided. These can be used to start up more complete locations in new locations. The equipment can be grouped into larger workshops and factories, or distributed across the membership. Most likely it will be a mix of both, according to local circumstances and what people decide is best. Starter locations begin with enough equipment to produce useful outputs, and start the upgrade and expansion process by making new equipment for themselves.
A more developed starting point like this needs a larger group of people involved, and if ready-to-use equipment is supplied, a way to pay for it. The R&D phase can supply the starter equipment as a product, which then funds more R&D. The members in the new location can pay for it by subscription or conventional financing. The new location members can also take the plans and instructions and build their own starter set, or take the plans to commercial fabricators to make for them. They can also use a mix of all of these methods. As experience is gained setting up and operating new locations, the information is fed back to the R&D phase to improve the designs and instructions.
- Phase 2A - Distributed Locations
As the network expands, and prototype equipment (seed machines) capable of making more equipment accumulate, members can start upgrading the percentage that is self-made and the scale of operation. Larger equipment needs more physical space and more inputs of materials and parts, and therefore more funding. At this point people can start up part or full time businesses whose revenue pays for further expansion. There are several approaches to such start-ups:
- Individuals can contribute some labor, tools and materials they already have, or money to the network. This establishes a balance they can use in a tool/production cooperative, small project, or a new business. The balance is an escrow amount which they can borrow against to use other tools and equipment. They would also need to pay a small consumables fee for items like drill bits or sandpaper, which wear out and need to be replaced. If they need to borrow an item above the value of their balance, or use an item for an extended time, then a deposit or rental fee might be added. That depends who they are borrowing from. A tool cooperative might not charge members rental. A completed project can be contributed back to the network to increase their balance, or they can use it in a business. For example, a project might be to build an enclosed utility trailer, which they can then use for moving furniture and office equipment for pay. They can also choose to contribute some use of the trailer back to the network so that other people can move tools and materials as needed, gaining network credit. So in this way they can bootstrap from a small starting contribution to a business.
- The network as a whole can operate as a set of physically distributed Nodes with distributed ownership, which coordinates tasks and payments between nodes. Each node performs one or more functions, like machining metal parts or ordering supplies - both for other nodes and for pay from outside the network. Within the network, nodes earn balances for future needs, shares in equipment or locations, cash, or a mixture. A business would then consist of owning and operating one or more nodes. Such businesses would grow incrementally as they add people, equipment, and more nodes.
A single Site may include multiple nodes who are close enough to trade on-site work and heavy items easily. An example is an industrial park with a mix of offices and production/warehouse activities. The cost and effort of bringing people on-site or moving heavy items increases with distance. Some number of sites within easy travel range of each other make up a Location. An example is a metropolitan area around a city. Network activity across multiple locations will be weighted towards remote labor and higher value-to-weight items. Sometimes bulk shipment can't be avoided. For example, if you are making lithium batteries for vehicles and energy storage, the lithium ore can only be found in certain places. In that case you can build and use your own transport nodes to move the ore, or hire transport from outside the network. Transport node vehicles are mobile by nature, but we can consider their location as wherever they are stored and maintained between trips. Roads and utility networks enable transport functions, but are not themselves mobile. They help link up nodes to each other and outside the network. Transport functions as a whole are required to enable flows of materials and products across the network.
- Phase 2B - Industrial Locations
The Phase 2A network as a whole grows by doing tasks and making things for each other, and at the same time selling products and services outside the network. Members can start up a new business as needed by collaboration. Eventually the scale of production and markets, and the equipment and staff to perform them, can grow large enough to be considered industrial level. We define a second sub-phase, 2B, for industrial locations, because the size and methods of operation would need different designs than the 2A distributed locations. For example, if large amounts of local rock are needed as building materials, the expanding production network can make some heavy duty mining robots and transport trucks. Some of the members of the network can run that equipment as a quarry. This is an alternative to conventional methods of starting a large business, like venture capital and bank loans. The larger the network gets, the more resources it has to create such larger start-ups.
There is no hard line between distributed commercial-scale and industrial operations. We can, however, identify some indicators of industrial scale. One is an operation large enough to need a dedicated site for that activity. Another is supplying markets beyond a single location and competing with other large operations of similar types. A third is equipment that is more heavy duty and is designed for full time use over with a long operating life. We expect that activities will evolve from home and hobby scale to commercial and industrial scale over time. However not every activity will grow that much, some will stop at a given size.
1.5.0.2 - Financial Model
[edit | edit source]
Operating the network will involve some money changing hands, so we use a financial model to describe how these money-related tasks are accomplished. One way to do them is by specialized network nodes for financial functions. They take initial funds and continuing subscriptions from project members and outside investors. These are used to set up asset pools. The pools can contain conventional investments, like stocks and real estate, and network assets like factory buildings and equipment. The members and investors form partnerships to own the asset pools. The network can produce new assets, like an office building or a machine shop, which are added to the asset pools. Their ownership is divided between the outside investors and project members according to their relative contributions. Conventional investments in the pools have the purpose of accumulating capital and income streams for larger network efforts, like purchasing land for development. They also serve to produce some returns until higher returns are available from within the network.
Automation is an important part of the project. So another way to handle financial operations is by using programmable currencies like Bitcoin. For example, creating a partnership can be done by designating a bitcoin funding address, plus mailing and email addresses. People wishing to join send their contact information to the latter addresses, sign a partnership agreement, and sending funding to either the bitcoin or mailing address. Since bitcoin maintains a distributed public ledger of all transactions, partners can monitor partnership activities at all times.
At a finer grain of operation, work to be done within the network can be paid for by posting an amount in bitcoins to an escrow address. The entity hired to do the work can see payment is available, but cannot claim it until their work is complete. Ordering a metal part can be done by sending the digital design files and the escrow address to the machine shop. Their software can verify the part can be made, and fits in their schedule, and accepts the order. Once the part is finished and delivered, the funds are released from escrow automatically. Ideally all of these steps can be automated and taken care of by suitable software. This eliminates much of the "front office" business overhead in conventional production.
1.5.0.3 - Unconsolidated Ideas
[edit | edit source]
The following are some business ideas to incorporate into the project models, but need further work to flesh out and incorporate:
- The larger the pool of equipment and assets, the more a network can make for itself rather than buy, and the closer to raw materials they can work from. Automation, process integration, self-bootstrapping, and capturing more of the value chain might drastically lower costs compared to conventional methods.
- In the US, work done for yourself using your own equipment is not counted as income, and therefore you do not owe income tax. This can generate higher return than working for others for pay. We don't know the tax situation for other countries, or if the benefits of self-work are enough to justify doing it.
- An automated market and payment network could allow you to efficiently buy or lease assets and resell them as needed. For example, you could lease the machines in a robotic woodworking shop long enough to make a piece of furniture for yourself. Since you made it yourself, you don't owe tax on it, and the shop doesn't owe sales taxes because they didn't sell you anything. The shop has rental income, but that has some tax advantages.
- It may be possible to use shared ownership and shared outputs as "tenants in common", with the ability to direct production, to preserve the "done for yourself" tax treatment. A simple example is shared ownership of a robotic farm, where the food grown is distributed to the owners. Not everyone wants to *operate* a farm, so perhaps the farm operator owns a larger share in return for their specialized labor, but the other owners still contribute to decisions on what to grow, or their own specialties, like accounting. We don't know how far this kind of "done for yourself" treatment extends.
- Cooperatives and non-taxable associations may be other methods to lower taxes. Existing examples are farm and electric cooperatives, and credit unions.
- Shared ownership may save on fees from high-overhead transactions like real estate and investments. For example, if a group can buy property outright, they can avoid loan origination fees. You have to be careful not to create a secondary security from passive investment, though. That creates a whole new set of overhead costs.
1.5.3 - Financial Plan
[edit | edit source]The project's founder is contributing his own property, tools, and materials, and up to 20% of investment income to the project. Outside contributons via a crowdfunding effort plus personal savings supply a funding base to begin developing an R&D location. When we get additional active project members and work out tasks and spending needs, we will develop a financial plan and record it here.
1.6 - Project Operations
[edit | edit source]1.6.1 - Schedules & Tasks
[edit | edit source][TBD]