The Seed Factory Project
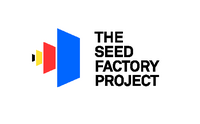
- 2.0 - Systems Engineering Technical Tasks
Systems Engineering is a cross-discipline field that focuses on complex projects, which our Seed Factory Project certainly qualifies as. It is performed in parallel with overall project organization (see Section 1.0), and with design, manufacturing, and other engineering tasks (see Sections 3.0 and later). It is not performed in isolation, but rather constantly interacts with other engineering specialties, both providing and receiving data from them. It also interacts with entities outside the project. This notebook is organized linearly, as a series of numbered sections for the various project tasks, but the parallel and interactive nature of the work should be kept in mind. The Systems Engineering sections of the notebook are distributed over multiple pages due to their length.
The general systems engineering process is a sequence of steps which are repeated at increasing levels of detail until a final design is arrived at. It begins with inputs of goals, objectives, and design requirements (section 2.1 below). These can either come from outside sources, are developed internally, or a mixture. In our case, the original idea came from considering future space projects. It has evolved into a general approach for solving some of the problems of current civilization. It fits into a larger program to upgrade and expand that civilization. The inputs then come from the today's unsatisfied needs and problems. As inputs, they are typically too vague to design to, so the next step is analyze them and put them in quantifiable and measurable form (2.2). This tells us specifically what the final design is supposed to do. We also identify how to prove the design actually does those things. Methods of proof include inspection, test, and others. Next we develop concepts, scenarios, and candidates to meet the requirements (2.3). This includes size and performance levels, and simulations and models to estimate how well it will work.
We then have to evaluate and decide which are the best candidates and their features (2.4) Generally there are trade-offs among requirements. For example, increased safety or operating life may also increase cost. So the right balance must be found, according to the original goals. There are also a number of specialty areas that need to be considered. These include how it may fail, how you maintain it, training needs, and others. Once requirements are defined and design choices made, the next step is to record the information developed so far (2.5). This serves as a baseline for further work, both in the systems engineering cycle, and by other specialties, for review by people outside the project team, and for final documentation. The last item falls outside the main engineering loop. It is support of the later stages of the life cycle, after manufacturing (2.6). This includes planning and procedures for final testing, acceptance, delivery, installation, checkout, and system configurations. Once a system is operating, feedback on problems and desired upgrades is returned to the project engineering team, and gets incorporated into a new design cycle.
2.1 - Initial Project Definition
[edit | edit source]Project Definition includes inputs to and outputs from the project to outside entities, and internally developed goals, objectives, and requirements. These serve as a starting point for the engineering and design process. Projects rarely spring forth with no background. The idea of self-replicating machines or factories has an extensive theoretical background, but it is only recently that technology has improved to the point they could be considered seriously. Replication implies more or less exact copies. The seed factory concept extends this by making new and different equipment (diversification) not in the starter set (seed), and making larger or smaller copies of previous equipment (scaling). The seed is only able to make some items internally. As the seed matures into a full factory, the percentage it can make itself increases, and less has to be supplied from outside. Our starting points include the background and past work on these ideas, and also the existing state-of-the-art in other areas of science and technology.
2.1.1 - Project Objectives & Requirements
[edit | edit source]
2.1.1.1 - Project Needs
[edit | edit source]
This section addresses the question "why do we need this project?". Project needs usually come from external sources who have problems they want solved. In our case we are starting with the problems of material scarcity and job insecurity in current civilization. We think that seed factories are a solution to these problems. They might not be the best solution, but we won't know that until we have done the work to find out. The reason we think they are a solution is their ability to copy and expand themselves in an exponential way, including the energy and raw materials sources needed for their operation. So a small input to build a starter set can provide a large result in final products. The large amount of outputs can then be applied to relieve scarcity. If the outputs meet people's needs directly, and production is highly automated, it reduces the need for conventional jobs.
We think the potential gains are large enough to at least start a project to explore the concept. Since the ideas involved are relatively new and untested, we must first do the necessary research and development (R&D). Then we can foster networks and locations to demonstrate the designs actually work. Assuming they do work, by open-sourcing the designs, other people can copy them as needed, multiplying the benefits. The networks and locations can supply revenue and equipment to continue R&D work on additional machines, improvements to existing ones, and applications to new kinds of locations and environments.
Material scarcity, as we use the term here, means not enough material goods for a safe and comfortable standard of living. For example, as of 2014, one third of the world's population still does not have improved sanitation. The seed factory approach to the scarcity problem is using self-expanding and highly productive systems to make enough for everyone's needs. Ideally the products would be made locally by the people who need them. The term "post scarcity" is sometimes used, but even automated factories will leave some scarce goods, like beachfront property and gold. What automation can do is enable everyone to have at least a certain level of goods, and reduce the working time to obtain those goods. We don't think we can satisfy 100% of what people need and want with current technology, so we would start with the basics. People can satisfy the remainder of what they need and want the way they do now.
Job insecurity has been present throughout history. For most people, work isn't desirable only for itself. Whether subsistence farming or software development, most people work to satisfy their basic needs, and some desires beyond those needs. Basic needs are things like food, shelter, and clean water, which are necessary to live. Desires are things people want, like entertainment and personal grooming, but are not required to live. Job insecurity or displacement is then a problem because people can't meet these needs and desires. The seed factory approach is to use automated production to satisfy those needs directly. If people own the equipment themselves, then they do not depend on someone else to supply them. In the near future, automation and robotics owned by large organization may add to the problem of displacing workers on a large scale. Via seed factories we can use the same automation that causes the problem to help solve it.
In solving the problems of scarcity and insecurity, we don't want to create new problems or make other ones worse. So we identify other project goals besides high volume automated production. A factory will consume raw materials and energy, and emit waste products. If done on a worldwide scale, we don't want to create resource shortages or pollution problems, a feature called "Sustainability". Our designs should therefore use common or reproducible materials and renewable energy sources when possible. We should also try to use wastes from internal processes, or from civilization at large, as inputs to other processes. This minimizes net wastes, or might even make it negative (the project leaves things cleaner than when it started). We also don't want to create or increase hazards to project members or outside entities, so "Safety" is an important goal.
2.1.1.2 - Project Objectives
[edit | edit source]
We use the term "Factory" to mean a set of people and equipment who work together to make desired products. Historically, the limits of communication required the people and equipment to be concentrated in one place. We still may concentrate factory operations for efficiency, but modern communication allows people to work remotely, and automated equipment to coordinate with each other from a distance. In the limit, the people and equipment may be entirely distributed. So our definition of a factory is based on working together for a common purpose rather than a building in a specific place.
The distinguishing feature of a seed factory is growth to a mature state by making more of itself, but that is not the sole purpose. We want certain outputs to satisfy human needs and desires. The outputs from a mature factory determine what equipment it needs. In turn, that final equipment list determines what the starter set has to grow into. So the design objective is a starter set and growth path that leads to a mature factory with the outputs we want. The growth path uses the optimum amount of self-production, according to how we define "optimum" (fastest, least cost, simplest design, etc.).
Early Phases - The project started with one person and a small amount of funding. We don't expect a massive team and large amounts of funding to appear right away. So we divide the project into a sequence of phases of increasing scale and difficulty. The early concept and design work can be done electronically, and doesn't need large amounts of physical resources. Once we start building hardware, we use some of the production from an earlier phase to make starter sets for the next. We gain experience from previous phases, making it easier to attempt the later ones. We also sell surplus production to generate funding for further R&D and to buy items we can't make internally. The phased approach is more feasible for a new project than trying to develop everything at once. So a further project objective is for each phase to lead to the ones that follow. We have identified a sequence of early phases and their goals. As we do more work, we may revise the sequence, but for now they include:
- Phase 0 - Research and Development (R&D): This phase does the necessary design and testing of new equipment types and production methods. The main output of R&D is information in the form of finished designs and ready-to-implement processes. The information is distributed elsewhere in the project and to outside users in the form of reports, handbooks, and design files. Materials, parts, and products are made during testing but are not the primary goal in this phase. They are used internally, sold, or delivered to later phases as practical and appropriate. Some sales of surplus outputs will help to cover R&D expenses. R&D funding also comes from contributions from project members, and funds from later phases to develop further improvements. Prototype equipment produced during R&D will be designed for useful operating lives, and will likely last longer than is needed for testing. So they may also be delivered to later phases if not needed internally. Operating experience is accumulated in later phases by using the prototypes and final designs. This experience is fed back to the R&D phase to make improvements. Distributed and independent R&D is encouraged across the project, but at some point you want to integrate and automate multiple machines and process steps. Therefore it will likely be necessary to build and operate R&D locations, with sufficient office, workshop, and test space for those purposes. These facilities must themselves go through a life cycle and can be designed using systems engineering methods.
- The R&D phase can be divided into sub-phases, according to the later phases the work is targeted at. Examples are R&D for starter locations, or R&D for industrial locations. In addition there is unique R&D for the R&D phase itself, such as special test methods that don't exist yet, or custom design and analysis tools. There may not be too much of that, since engineering research and development in general is a well-developed field. Finally there is generic R&D about seed factories, which applies to multiple phases and location types. The unique needs of later phases feed back to the R&D phase as requirements. Along with them will be requirements imposed from the overall project goals, the wider program to upgrade civilization, human constraints such as laws and regulations, and physical constraints from the outside world.
- Phase 1 - Starter Locations and Network: Starter locations begin with conventional tools and equipment, and people start to make items for themselves and each other at a personal production scale, for hobby and home use, but less than full time occupations. A starting point might be a tool cooperative or community workspace. Prototypes and final designs for seed equipment are gradually supplied from Phase 0. The first seed equipment is made using conventional tools and machines within the project, sent out for fabrication, or parts are ordered as needed. The seed equipment allows the network of people to increase self-production, and start to upgrade their other tools. The equipment is small enough in this phase to include multiple pieces in a home or shared workshop. To reduce starting costs and physical space required, early seed equipment is optimized for flexibility rather than speed or quantity of output.
- Planning and design for Phase 1 and later phases is done in reverse, from desired outputs to necessary inputs, but then implemented in the forward direction in logical order. The desired outputs in this phase are (1) a network of people and equipment who can produce and trade items at a personal scale. Designs, small items, and remote labor and help can be traded worldwide, while heavy items and direct labor tend to trade a smaller distance. (2) With help from R&D locations, the capacity to spawn new locations and starter sets at the personal scale. These get added to the overall network. (3) Along with R&D locations, the capacity to make starter sets or individual machines sized for Phase 2A full time distributed or 2B industrial locations. Phase 2 equipment only has to be the minimum useful size for those purposes, with further growth to mature scales in the later phases.
- From these outputs, we work back to identify and design the necessary facilities, hardware, software, people skills, processes, and training needed to produce those outputs. These items are then organized into a project sequence by a combination of personal desires, funding, and logical scheduling. Finally we identify the starter and expansion set elements for the phase based on this sequence, including parts and materials that need to come from R&D locations and outside sources. A complete starter set for Phase 1 may include a mix of manual, portable, and stationary commercial tools and machines, prototype and final seed machines, parts and materials, and designs and instructions for what to make in what order. Rather than being provided all at once, early starter sets will likely be accumulated over time. As R&D and the network operate and grow they will be more able to deliver complete starter sets.
Phase 2 - This phase includes growth beyond hobby and home scale production. We divide it into two sub-phases according to the scale of production:
- Phase 2A - Distributed Locations: As the Phase 1 locations and network develop, people can choose to spawn small business and commercial scale operations in multiple distributed locations. This goes beyond personal or internal network use, and involves selling to the general public, and part or full-time operation. It would typically use larger or more copies of Phase 1 equipment. Larger and more copies are two of the planned expansion paths for starter sets in general, along with making new kinds of equipment. So these locations can be largely self-built internally by the network. Network nodes in this phase tend to be larger and more specialized as they are used more intensively and commercially.
- By late in this phase, the network as a whole should be able to supply most of the needs for food, shelter, and utilities of a local community by means of locally owned enterprises. These needs are basic ones that everyone shares, so we hope this phase will have widespread application, especially for people who don't have these needs fulfilled today. A community can be purpose-built in a single area, on the scale of a suburban subdivision, or it can be a subset of interested people in a larger population, such as a US county or metropolitan area. What defines the community size is the variety of tasks and skills needed, efficient scale of operation, and number of different equipment types.
- We think that meeting 100% of a community's basic needs is too difficult for a first generation design. So we set an initial goal of 85% of their food, housing, and utility needs, with community members filling the difference with outside work and outside supplies. That lets us design for the simpler, easier and more commonly used items first. The more complicated or difficult items are deferred to later generation designs. Because of self-production and automation, the bulk of community needs would be met with less cost and less work than conventional alternatives, giving people a reason to participate.
- The previous phase was designed mainly to grow itself and spawn new locations and starter sets, plus make some products for hobby and home use. This phase continues the ability to grow, but increases the scale to business and commercial. The range of products is widened to support most of people's basic needs, plus whatever other products can support part or full time business. As before, we work backwards from the size and types of outputs, to what is required to make them, and then a growth sequence from this phase's starter sets. R&D and Phase 1 locations are still in operation, and the latter may evolve into this phase. The other phases can serve to supply some parts, materials, and equipment for this phase, and less is needed from outside sources. Planning the starter and expansion set sequence for this phase will therefore incorporate the capabilities of previous phases. We cannot plan out every detail of the growth path. For example, we don't know what people will join the project or when, and what their skills will be. The plans should be modular and adaptable to circumstances within a framework of eventually reaching the end goals of the phase.
- Phase 2B - Industrial Locations: Phase 2B continues the growth in scale of Phase 2A from satisfying needs of a local community to metropolitan or larger scale. It also increases the range of products beyond those frequently needed by a local community. The market for the products must therefore be wider, and more of the outputs are sold outside the network. Industrial locations are large enough that they may need outside capital or extensive growth cycles. They tend to be more specialized, because fitting a large assortment of large equipment in one place becomes difficult. At the same time, a limited product range exposes the location to more variation in demand. Distributed ownership makes sense in this case, versus direct owner/operators on smaller scales. Demand for a given product can fluctuate, but other products are likely to balance them out. Labor and equipment can then be shifted or modified as needed among a network of multiple owners.
- There are approximately 2700 categories of products and services across a developed economy, and our project cannot hope to design for all of them. Our approach is to find common starter equipment that leads to a wide range of mature industrial locations. Mature industrial means on a large enough scale to capture most of the economies of scale, and serve metropolitan (100,000 population) or larger markets. We use the U.S. Census Bureau Industry Classification System as a source list of categories. We then select a broad sample of 50 of them, and determine the necessary facilities, hardware, software, processes, and human skills needed, when operating with advanced automation at an industrial scale. As with previous phases, we then work back to what is required to make those facilities and other items. That includes both production quantities and equipment used internally, and outside supplies. Finally we plan a sequence of starter and expansion sets that lead to the desired end points. Previous phases still exist, so their capacity and outputs should be included in this phase's planning.
- Since the phase as a whole is producing for many industries, the starter and expansion sets from each can be combined and scaled to support all of them. By examining the individual starter sets, we may find shared items used in many of them. This results in copies of a generic starter set, with modifications or additions for a particular industry. Alternately we may find a wide diversity of starter set equipment by industry. In that case, a general industrial starting point with a wide variety of equipment makes sense. It would mostly grow by scaling, until the outputs are large enough to support a range of industrial locations. We won't know the best approach until we have done more work.
The early phases are defined by their objectives, leading to different output categories, production scales, equipment sets, and growth paths. Their designs will differ, but the design process will be similar for each, because all of them involve self-growth from starter sets to mature production systems. Phases are linked in that outputs from previous phases are used to help build later ones, and a given location can evolve from one phase to another by expansion and upgrade. Note that phases are not disjoint in time, but overlap. A new phase can start before previous ones are complete, and previous phases can continue to operate indefinitely in parallel with later ones.
Later Phases - To this point the phases have been similar in terms of their moderate operating environment and proximity to populated areas and infrastructure. Beyond Phase 2 we move into locations that are remote, undeveloped, and physically different, such as the oceans, ice caps, deserts, underground, and beyond Earth. These locations can't evolve from home workshops because there are no homes to start with. The later phases require transporting custom starter sets from earlier locations rather than evolution and growth in place from existing populated areas. We have identified several of these later phases by relative difficulty. We plan to defer the detailed design work for them until there is some experience and a production base to build on from the earlier phases.
- Phase 3A - Difficult Earth Locations: These locations have one or more characteristics that make deploying and operating a starter set more difficult than in earlier phases. One is remoteness from other populated areas, requiring transport of equipment, people, and supplies long distances. Another is low or no development, so lacking infrastructure like roads, utilities, and communications. Third is physical differences in their environment, such as swamps and ocean surface, which have low or no ground strength; polar regions and hot climates, which have temperature extremes; rain forests and deserts, which have too much or too little water; and being underground and having to excavate and support high pressures. Difficult locations can be chosen for resource advantages, such as plentiful sunlight or wind for power, or specific materials to extract. They can also be chosen to relieve overcrowding and high costs in overdeveloped areas, extend food production to new areas, and compensate for losses from environmental change. Lastly, people may just prefer a particular location to live in or visit, and high levels of automated production can enable this.
- Designing for these types of locations is similar to the previous ones, but must account for the more difficult operating environment and longer transportation distances. Because of the higher cost of long-distance supply delivery, the designs would emphasize using local materials and energy, and more self-contained starter sets. By means of self-expansion and automation, using these more difficult locations would be more feasible than today.
- Phase 3B - Extreme Earth Locations: These locations require assistance for normal human life. It includes very tall mountains and high altitude structures, which have low air pressure; underwater, which has no breathable air and high pressures; and deep underground, which has high ground pressures and temperatures. Between merely difficult and extreme is a matter of degree, so specific parameters will be defined to distinguish them. Because people can't work under extreme conditions, you either need to send automated or remotely operated equipment first, or supply all the needed life support equipment, like oxygen masks, submarines, and powerful cooling systems.
- Phase 4A - Low Earth Orbits: These locations are between 100 and 2000 km altitude. There is essentially no air at these altitudes, so aircraft cannot operate, and merely compressing outside air like you could on a high mountain is not sufficient. To maintain orbit, you must have enough sideways motion (6.9 to 7.8 km/s). So locations are not fixed like they are on the surface. The motion balances gravity and centrifugal acceleration, so you are in free fall (no relative acceleration between objects). This is mistakenly referred to as "zero gravity", but the Earth is nearby and still has a strong gravitational force. It is just balanced by an opposite acceleration from motion. Sunlight is more intense in orbit because there is no atmospheric absorption. There is also hazardous radiation, and typically strong thermal cycles from crossing the Earth's shadow. Very little local matter is available to build with, so most supplies must be imported from elsewhere.
- Reasons to build in orbit are evident from the over 1250 active satellites already there. Self-expanding production can lower the cost of goods and services in orbit, and returned to Earth. Lower costs would likely expand the range and scale of space industry.
- Farther Space, Planetary, and Beyond: The idea of seed factories was first developed for remote space locations, because bringing everything from Earth gets increasingly expensive the farther you go. So the benefit of making items using local materials and energy is strongest there. However, most needs that people have today are here on Earth. We will keep in mind future applications in space, but defer most of that work to later. It should be noted the two are linked together. Most of the actual work for current space projects happens on Earth - in offices, factories, launch sites, and control centers. Earth-based production capacity can be adapted to make the buildings and equipment for these locations. Launch systems made on Earth can be used to deliver seed factories to locations in space. The factories can be operated remotely, from Earth or a previous space location, until enough human needs can be supported for residents to arrive. A flow of supplies and hard to make items will continue to come from Earth as long as needed, and space-based production can supply needed products, services, raw materials, and energy back to Earth. Space is not this "other place", disconnected from earthly life and concerns. Rather, it becomes an extension of our expanding civilization.
2.1.1.3 - Project Requirements
[edit | edit source]
The needs and objectives from the previous two sections are too vague to design to. So in this section we provide top-level project requirements in more quantifiable and measurable form. A requirement is a carefully worded statement of what the final operational system will or will not do, often including numerical values. For example, "Output shall be at least 100 tons of crushed stone per day." is a requirement type statement for a rock quarry. This tells us one of the features the final design has to meet. We can easily tell if the design, and later the operating quarry, meets this requirement or not. With a more vague objective like "Mine our own rock", you cannot tell if you have met it well enough to satisfy needs elsewhere in a project. In a later technical task we will break down the top-level requirements to lower levels, and assign them to parts of the design. At the lowest level a small subset of the requirements apply to a single machine or component. A person or small team can design at this level of complexity. The entirety of the project is too complicated to be designed all at once, but the parts must work together. Flowing down requirements from the top, then step-wise integration of smaller elements into larger wholes is how complexity is managed. Each step in the process then becomes less complicated, and reasonably skilled people can accomplish them.
[To Be Done - Adapt requirements from Seed Factories and Space Systems wikibooks]
Project Description
The Seed Factory Project (SFP) is part of a larger program to upgrade and optimize civilization. The larger program is intended to fix current problems and deficiencies in order to maximize happiness and meet long term goals like safety and sustainability. The SFP's primary purpose is to address the material scarcity and job insecurity problems of the present and near future. The Seed Factory concept is to use self-upgrading production systems that grow from a starter set, like the way biological plants grow from a seed. At first, the seed machines do not cover every product and task, and need more human labor and outside supplies. As the collection of machines grows, they implement more automation, and are more able to make parts and materials for their own growth. Eventually they are able to make new starter sets, and replicate the growth process. In principle a single seed factory can grow to become an unlimited amount of production capacity. In practice, though, something will limit this growth. New starter sets can have different purposes and operating environments than the previous generation, and later ones can incorporate experience from earlier ones. So the contents of a starter set will change according to circumstances and experience. Once there are multiple locations and a production network, they can supply more parts and materials to new locations, so that expansion past the starter set can happen faster and at lower cost.
The "reproduction cycle" from starter set to another starter set is roughly estimated at 3 years in an average location on Earth. This equates to a 26% annual growth rate. Such high growth rates make it possible to solve scarcity and security issues by producing most of what people need. Every product, including more factory equipment, has an "embodied energy" which is all the energy used in creating the product. The available energy to run the production equipment therefore limits the growth rate. So a general growth rule is to make more energy supplies first, in order to power the remaining systems, and to keep a high ratio of power sources to factory mass as you grow.
Our intent is to have the factories owned by people who use the products they make. There are several reasons for this. One is that when the owners are a distinct class from the workers, like shareholders are in many modern corporations, getting rid of workers lowers costs and increases profits. This creates job insecurity. When the owners are the same as the workers and users of the products, their interests are aligned. They don't have an incentive to get rid of themselves as workers, but they do have an interest in making themselves more efficient through automation. That way they can work fewer hours or increase output, as they prefer. Self-ownership does not eliminate the need for specialization. So production may be organized as member cooperatives, or networks of individual businesses who trade different products. It also does not eliminate the need for start-up or expansion capital. But passive outside capital whose only motivation is higher profits should not be the sole owners, to prevent the dissociation of interests noted above. There should be a strong component of worker and user ownership.
Other reasons for self-ownership are human dignity and economic security. Income transfer by way of a Universal Basic Income has been suggested as a way to address automation-induced job displacement. Another possibility is government-owned factories that supply goods. This makes recipients dependents of the State, who might withdraw payments or deliveries for any of a number of political or legal reasons. Whoever is being taxed to fund the government programs naturally wants to reduce their taxes. Even if people being taxed are also recipients, there will always be a group who pays more than they get, or else the system is pointless. They would therefore agitate to lower the tax rates and payouts, making the system insecure. If such programs are not universal and worldwide, those who pay the most to support them have an incentive to flee to places where they are not used. Flows of free money or goods, and higher marginal tax rates, reduce the incentives to produce for some members of society. This lowers overall output, making society as a whole poorer. When people get the full benefit of what they produce, they have more incentive to do so. We recognize that some people are disabled, sick, or otherwise unable to contribute to their own needs. There will still need to be systems in place for such people, but if they own a share of production, they can be partly self-supporting even if they can't work.
2.1.1.4 - Operational Concept
[edit | edit source]
An operational concept describes "how it works" internally, where requirements describe "what are the results" when viewed from outside the project. In general, the operating concept for a seed factory is to take in materials and parts, and follow prepared designs and instructions to produce various outputs. These outputs can be split into three groups: (1) useful end products, that fill people's needs and desires directly, or can be traded for other products, (2) items used for internal growth and maintenance, and (3) items to seed new locations and later phases. The fraction devoted to each part can vary over time. So a new location may put more into growth and seeding early on. Once a location reaches maturity it may shift to mostly end products. Production can be repetitive, making the same items multiple times, on-demand as people ask for specific things, or some mix of the two. Automation allows changing outputs quickly by loading different design files, similar to how computers can easily run different software by loading and running it.
Setting up the first seed factory in a given location requires outside supplies of labor, tools, equipment, materials, and funding. Over time it becomes self-supporting by producing more output value than the inputs required, although it may not do so right away. People who wish to join a network or start a new location can follow one of two paths. They can use or buy equipment from the existing network of locations, or they use project designs to build their own versions from scratch, with adaption to local circumstances. Useful products may be used directly by owner/operators, they can be sold in trade for other things people need, or to pay for inputs the factory can't make. Factory operation is by a combination of direct hands-on labor, people controlling equipment remotely, and automatic and software control. Besides intended outputs, a factory will also produce waste outputs like heat and scrap materials. By design we try to minimize final waste outputs. For example, excess heat from a furnace may be used to heat water or warm a greenhouse, rather than simply dumped. All inputs, outputs, and internal flows are tracked by resource accounting. This is like financial accounting, but applied to all types of resources and not just money. By tracking resources, we can optimize the designs and make sure we don't create unintended waste problems.
Once a new phase is started, the locations for that phase continue to operate as long as needed, in parallel with other phases. So after the first generation of equipment is demonstrated, the R&D phase would continue to improve the technology and performance of existing equipment, and develop new equipment for later phases. The directions for improvement include higher percentages of self-production and automation, simplifying and optimizing the starter set, and adapting the seed concept to more difficult locations. Starter locations making items for personal use can continue to exist while larger commercial and industrial ones grow, and so on. Equipment wears out over time and requires maintenance to keep operating, and upgrades to newer or better equipment can happen at any time. So a mature location must still have the ability for maintenance, repair, and replacement. Maturity indicates an intended capacity or range of products has been reached, but not that it has become fixed and unchangeable. By analogy, a mature tree continues to grow, but it is past the rapid gains in height and volume of seedlings and saplings.
People buy or build enough automated equipment to satisfy their needs directly, or trade with others if they are specialized. In that way, the transition to a fully automated society does not leave people unsupported, or subject to the whims of a third party who may not have their best interests at heart. Particular factories may be designed for different outputs, and function in different operating environments. The contents of their starter sets and expansion plans will therefore vary, but they all share the feature of growth by self-expansion. Factories can trade products with each other as needed.
A given location or production network may include some or all of the main categories of service, production, habitation, and transport functions. Within the main categories it can include any subset of specific industries. Whatever functions are needed, but not included in a given location, are then supplied by other locations, or from civilization at large. The production function generally includes the following shared elements, regardless of where they occur:
- Monitoring and control of the production processes
- Energy supply for the various processes
- Growth of organic items
- Extraction of raw materials
- Processing those materials to a ready-to-use state
- Intermediate and final storage during production
- Fabrication of parts from ready materials
- Assembly of parts and materials into complete equipment
2.1.1.5 - Operational Environments
[edit | edit source]
Operational environments describe the local conditions the people and equipment have to withstand. When the conditions are not suitable for the task at hand, like doing office work in a rainstorm, it generates a need for protection from and modification of the local environment. The locations for early phases of the project: R&D (0), Starter (1), Distributed (2A), and Industrial (2B); are intended for moderate climates near existing populations and developed infrastructure. These are easier starting points than more remote or climatically extreme locations. The term "moderate" we use to include more than just temperature range. It includes other environmental factors like rainfall, sunlight, air pressure, and ground strength. We define "near" as within a couple of hours of a population center, and preferably less. This allows reasonable travel time among network members, and for people doing hands-on labor away from home. It also provides for reasonable delivery of supplies, and outside services and products. Infrastructure includes at least roads and communications, and preferably water, electricity, and sanitation. As we build experience and production capacity we can supply more of these items internally. The need to be close to existing population and infrastructure will then decline.
The locations for later phases: Difficult Earth (3A), Extreme Earth, and beyond Earth (4A and later) are progressively farther from existing populations and infrastructure, and the physical environment diverges more from moderate conditions, to the point of being hostile to life as we know it. About 87% of the Earth's surface is ocean, desert, or ice cap, and is mostly unused. We rarely use vertical heights more than a few hundred meters above or below the surface of the other 13%. Seed factories and their related technologies can allow us to move beyond the limited and thin patch of Earth most of our civilization occupies, and benefit from the added physical space and their resources. Remote operation and automation allows new locations to be developed before lots of people try to live there. Local energy and materials reduces how much has to be brought from elsewhere. This becomes especially important for locations beyond Earth.
Starter sets for these later locations are optimized for remote operations and use of local resources. They are supplied by networks and factories from previously existing locations. For example, an ocean platform may be delivered from a nearby coastal location.
2.1.2 - Project Outside Documentation
[edit | edit source]
Outside documentation includes data going to outside entities, data coming in from outside sources, and data about the boundaries of and connections to the project from outside. It includes the assumed baseline, or starting point from previous work, requirements supplied from outside the project, constraints and fixed requirements imposed on the project, external interfaces, applied standards, and external inputs from engineering specialties.
[Most of this information is to be supplied later, except for the initial baseline.]
2.1.2.1 - Initial Baseline
[edit | edit source]
A "baseline" is a starting point for the current design work to build on. Our current baseline comes from past work in 2012-2013, in the first round of concept exploration. Further work has gone into the seed factory concept since then, including a lot of online discussion, and the purchase of a property for R&D, but this has not yet been incorporated into a new baseline.
Core Functions
We identified certain core functions that any production system needs to produce useful products, provide maintenance to keep operating, and grow to a larger and more diverse industrial capacity. Traditional factories tend to be specialized in what production steps and products they make. For these factories, many of the functions are supplied from outside. Self-expanding factories and production networks do more of these functions internally to raise efficiency and better automate. The core functions include extracting and processing raw materials, supplying energy to operate, fabricating mechanical and electrical parts, and assembling them into end products and new production elements. In addition to these, there is normally monitoring and control of the various processes, and storage for items not being worked on. Sometimes there is growth of organic items, who perform most of the core functions internally.
Starter Set
Approximately 300 known production processes exist across all industries. Not all are needed in the starter set of a Seed Factory. You only need enough to start the growth process. Any other processes are at first handled by outside parts and supplies which already incorporate them, or purchased services to perform them. As you build more equipment, you can gradually do more processes internally and need less from outside. A starter set should try to do as much as possible with the fewest pieces of equipment. We identified eight basic production elements, plus accessories and attachments for them, which we think are flexible enough to serve as a starter set. This set is our starting point. It may change as we do further work, especially finding starter sets for different project phases, locations, and end products:
- (1) Modular Robotic Vehicle and Attachments - which provides physical transport and manipulation. The robotic arms and their attachments can operate separately as stationary factory items, or attached to a vehicle. The robotic vehicle core can also operate without attachments for simple transport, or with any of a variety of devices like conventional farm and construction equipment use. The robotic vehicle can operate autonomously using cameras and sensors, and it's own computer and software. It can also be operated remotely under automated or human control. Larger versions can include an optional control station for manual operation.
- (2) Solar Furnace Facility - which provides electric power and high temperature process heating. Concentrated sunlight is a high quality energy source. Different target devices placed at the furnace's focus allow using the energy for different purposes like power generation, cement and brick making, and metals casting. A thermal storage bed can store excess energy for times when direct sun is not available. Other renewable energy devices, like wind turbines, can also supply power, but a furnace is a more flexible starting point.
- (3) Multi-Head Bridge Mill - which performs machining, 3D printing, plasma cutting, and other functions. The bridge has mountings for up to four different working heads, each of which can do a different task. The heads, in turn, can be exchanged whole, or swap bits or supplies at the sides of the frame. The shared bridge frame provides vertical (Z axis) and cross motion (Y axis), and rails for a translating platform provide the X axis. The variety of functions and size of objects are only limited by the number of different heads and length of the rails and tables which ride them, respectively. Additional motion axes, if needed are supplied by the heads and tables, and tables can be swapped for different tasks.
- (4) Quad-Rail CNC Lathe - which does more accurate and symmetric parts. Two rails support the main spindles and workpiece, while the other two carry a cross-slide, turret, and milling head. Since the four rails are rigidly attached to each other, high accuracy is possible. The rotation of the spindle makes the lathe better for round parts, while the linear motions of the Bridge Mill is better for rectangular shapes.
- (5) Four Post Hydraulic Press - which does all types of forging, molding, shearing, and rolling. A press is generally not as accurate as machining, but much faster, and suitable for preparing raw stock for final machining. The four posts guide a moving upper plate relative to a fixed lower plate, driven by a powerful hydraulic cylinder. A variety of attachments are fixed to the plates, like dies and molds, cutting blades, rollers, and auxiliary heaters if needed for hot forging.
- (6) Flexible Process Plant - which does a variety of physical, chemical, and electrical processes. Physical processes include things like grinding, mixing, and drying. Chemical processes involve reactions or catalysts, and electrical processes include items like electrolysis and plating. A variety of end products are made by connecting a series of units which do one step each in different sequences, and storing intermediate products as needed. The process plant starts with a limited number of units and possible products, which increase over time.
- (7) Electrical Shop - which produces simpler electric and electronic items, and assembles them into complete devices. Simpler items include wires, coils, filaments, batteries, transformers, motors, generators, and custom circuit boards. More complex parts like computer chips and displays are typically bought.
- (8) Modular Production Building - which provides the proper environments for operations, utilities distribution, structural support, storage, assembly areas, and materials handling. It also provides for human work areas, and access for maintenance. The building is designed to be easily extended and re-arranged as the factory grows. This is enabled by using standard sized "modules" for placement of equipment and utilities.
Each of the major elements can be extended with more units, attachments, tooling, and bits. Making such additions will be an early task for the seed factory. Nominally we would start with one of each of the core elements, but for higher production rates we can build multiple copies. It is also possible to start with conventional tools and just one or a few items from the starter set. An incomplete set would be less able to grow itself, but might be necessary due to available working space, budget, or during the R&D phase because their design isn't finished.
[Figure to relate core functions to starter set]
Additional Equipment
These eight major elements are not sufficient by themselves to operate or grow a factory. Additionally you need:
- Computers, software, and networking which control the automated operations,
- Design files for the starter set, and expansion sets of later equipment,
- People, which tell the computers what to do, remote control equipment, and perform manual tasks which are not automated, and
- Accessories like mounting fixtures, portable and hand tools, maintenance and cleaning items, shop furniture & storage, and items for measuring, sharpening, hand finishing, manual assembly, and similar tasks.
Growth Paths
The number of major pieces in the starter set is kept small by selecting for maximum flexibility rather than maximum efficiency. Later additions can be more specialized. For growth, the starter set can be used to build more copies of its own equipment, different machines to extend the range of processes or increase efficiency, or bigger machines to increase scale and production rates. Enough physical space is required for additional buildings, solar collectors, and growing organic products. Raw materials must either be extracted on-site, or come from nearby temporary sources. In it's most portable form, a seed factory can begin with no production elements at all. It would only consist of design files and instructions to build the starter set and later additions. Outside services can make the initial set of parts, or they can be made using conventional tools and equipment, like we plan to do with our R&D prototypes.
A factory or network will not make 100% of it's own parts. At first this is because it does not have the all the equipment required. Later on there will be scarce materials or complex parts, like computer parts, which are not economical to do internally. Instead the operators would sell surplus production to pay for items they cannot reasonably make. As the factory grows it will be able to make an increasing percentage internally. Our present goal for a first generation mature production network is 85% self-production, with later generations reaching 98%. A starter set will begin with considerably less than those levels, and grow to them over time.
The production system will not be 100% automated either. Current automation and robotics is not yet capable of doing every task. In addition, with finite time and resources to develop this project, we do not think we can design and program for every step. Finally, some tasks will only be done once or very rarely, so it is not worth trying to automate them. Therefore the you will need some people to operate equipment, either physically on-site or controlling the machines remotely, and to do whatever non-machine manual tasks are needed. Our goal for the first generation design is to automate most of the routine and repetitive tasks. With additional time and resources, more of the tasks can be programmed to run automatically, improving productivity.
We will use already existing conventional tools and equipment, and a conventional building, to make the prototypes and the first working version of the seed factory. Some of that may be done in distributed locations by project members or ordered from commercial suppliers, rather than in a central location.