The Seed Factory Project
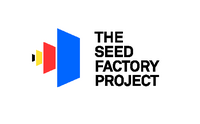
2.3 Design Synthesis
Design synthesis is the next major step in the systems engineering cycle. Once requirements are defined to a given level of detail (section 2.2), a design to meet those requirements must be developed. Most of the detailed design work is handled elsewhere (sections 3 and later). In this systems task we develop overall scenarios, architectures, diagrams, and interfaces. Working with with specialized engineering skills, we also develop a preliminary design at a high level, identifying major elements, their sizes and performance, and if the technical state of the art, suppliers, and available facilities can support the design. If not, it generates a requirement for research and development, production capacity, or site construction. Mathematical models and simulations are developed to enable analysis and optimization of candidate designs (the actual optimization is under section 2.4)
2.3.1 - Project Architecture/Preliminary Design
2.3.1.1 - Operating Concepts and Scenarios
[edit | edit source]Definitions
[edit | edit source]A MakerNet is a distributed network of people and tools that evolves to a mature production ecology by self-production and upgrades. The name is derived from Maker Culture, a modern extension of do-it-yourself culture. Makers typically are interested in electronics, robotics, 3-D printing, computer-controlled tools in addition to more traditional metalworking, woodworking, and handicrafts. Net is shorthand for any kind of network, especially the Internet. A MakerNet may use direct person-to-person contacts, and grow to use automated electronic collaboration via the Internet or other electronic networks. It may operate informally or with a formal structure.
For the purpose of design and organization, we define MakerNet Nodes as providing some set of services, production, habitation, and transport functions. Nodes regularly interact and communicate with other nodes in order to trade, provide assistance and training, and collaborate on projects. Nodes have ownership and control systems which may vary from individual, cooperative, or for-profit company.
The MakerNet as a whole may cover any amount of area, since modern communications function worldwide. Direct human work and physical equipment, however, requires increasing time and cost to move large distances. So we define a Location as a set of nodes close enough to easily work together. Roughly this can be thought of as a metropolitan area, or a region within 0.5 to 2 hours travel time. At the compact end, nodes may form a location in a shared building, industrial park, or intentional community. We expect the MakerNet to evolve to many nodes in multiple locations.
We can measure the percentage of self-production in terms of variables like mass, parts count, or economic value. A location or the network as a whole may start close to 0%. It will not be exactly 0% because any skills, tools, and equipment at all can be used to make something, even if a small amount. 100% self-production creates a closed loop, where network outputs can be fed back to supply all the tools and machines used in their own production. This is called full closure of the production loop, and lesser levels as percent closure. A fully closed production system can copy itself (replicate) if the rate of production is higher than the rate existing equipment wears out. If new production were less than wearing out, the system would break down due to not making spare parts fast enough. The history of technology across civilization shows new production > wearing out. If that were not true, we could not have accumulated all the factories and their products which exist now. Automation and networking of production should not decrease the ratio of production to wear out. In fact, we expect it to increase, because labor inputs will result in more final outputs.
We can also measure the percentage of automation in terms of production output per unit of labor input, which is conventionally called productivity. We can also count processes, production steps, or parts, and see how many are automated, vs manual or remote controlled by people. 100% automation is possible today for individual processes. For example, a refrigerator can keep food cool, defrost itself, and make ice without human intervention. But more complicated chains of processes and steps are not typically fully automated, either for cost reasons or lack of suitable technology. A goal of the project is higher levels of self-production and automation. Research and development will be needed to make that possible. Automation is already an extensive field of engineering, so most of our efforts will be in the areas of self-production and integrating a network of diverse nodes so they can work together.
Maturity of the production network is determined in one of two ways. First, individuals and groups may decide they have reached a sufficient level of self-production and automation, and stop making upgrades. Outputs are then directed at items to be consumed rather than internal improvements, plus any maintenance and repair required. The other way to determine maturity is by the current state of civilization and technology, and characteristics of the locations being used. The market for a given product may be saturated, or there is not enough physical space for factory expansion, so further growth in capacity would not make sense. Particular products may be too hard to make internally, or need rare materials not available at a given location. It is more efficient to trade things that can be made, to pay for these products that are too hard or can't be made, rather than attempt to make them internally. The network may already be using the best automation technology available, so further upgrades are not possible.
These maturity conditions are not static, though. New members may join the network with higher goals, markets may expand, or even be created by seeding new locations. New locations can also supply more working space and sources of different or rare materials. Enough experience and skills may make previously hard to make items easier. Technology in general, including automation technology, tends to improve over time. Part of that improvement is due to research, development, and experience of this project. Any decision not to expand or upgrade further is then subject to change for a number of reasons. In particular there are many locations beyond those with a temperate environment which are already developed and populated. These have lots of physical space for expansion and potential for development and upgrades. They also can supply new sources of energy and raw materials. At least 80% of the Earth's surface is undeveloped and low population, in the form of oceans, deserts, and ice caps. Underwater, underground, and high altitude locations are minimally developed, and space locations are both minimally developed and unlimited in size. So we don't expect limits to growth and upgrading unless people restrict themselves to already developed areas, and forego any remote or autonomous operations. We don't think that will happen.
Evolution and Operation
[edit | edit source]- People may start with no skills or tools. The first step is then to use libraries, the Internet, training by other network members, and other educational systems, to acquire some basic skills. People who have some tools can lend them informally to those who don't, or new people can buy some through conventional channels. People may form a tool cooperative, such as a makerspace, hackerspace, or community workshop, to distribute the cost and provide housing for larger and more expensive items. Network members may organize buying items in bulk or quantity discounts in order to reduce costs, then distribute the items as needed. This may require storage space for inventory not yet distributed. If some people have good income or savings, they may finance the initial cost of a location, which others can then use. Funding can also be on a subscription or donation basis. Some people may already have substantial skills, tools, equipment, or working space from an existing hobby, profession, or property they own. In that case they can contribute their use to the network.
- Starting a new location or setting up a node may require mobile tool sets. This can be accomplished with a standard vehicle with transportable tool kits, customized vehicles, or detachable trailers which can be brought to a work site as required. Established nodes and locations can grow in place using equipment they already have, but the nature of a distributed network will require moving a fair amount of people, equipment, and products between nodes. A node can start with just one function, and add new ones as it evolves. At a minimum it must communicate with existing civilization as an unconnected node, in order to obtain supplies and possibly sell products. As a connected node within the network, it can still communicate with civilization at large, but additionally with other nodes to trade and collaborate.
- Ownership of, and transfer of nodes to new owners, may be partial, such as partnerships or joint shares. The transfers may be manual or automated. For example, highly automated nodes may build a new node without human assistance, in which case the owners of the existing nodes become part owners of the new one automatically. Ownership may be centralized, where one organization owns many nodes, or distributed, where many people own nodes or parts of nodes individually. Control and operation of nodes can also be centralized or distributed, manual or automated, local or remote, or any mix of these. The choice of how nodes are owned and operated is according to what people want, and what makes sense technically.
- The evolution of the network is directed at increased self-production. This lowers cost by moving inputs closer to raw materials and capturing more of the value added by production. It also lowers dependence on outside sources of supply and conventional paid jobs. Evolution is also aimed at increased levels of automation. This decreases required labor and increases productivity and quality. The evolution is in steps that add new processes and equipment, and upgrades existing hardware and software. In theory this leads to factories that run themselves without human intervention, and produce everything you need from raw land and renewable energy. In practice, the state of technology is far from this ideal, but it gives us a direction for making improvements.
- Some tools and equipment may already exist that are suitable as-is for the project. However many will need to be redesigned so the network can make their parts internally, they can function automatically, and can function as an integrated set that aligns inputs and outputs. Continuing work will be needed to make these improvements.
Project Phases
[edit | edit source]- The evolution of the network and locations is more or less continuous, to larger scales, more difficult locations, and higher levels of self-production and automation. For design purposes we divide this evolution into phases, since the equipment required will be different sizes, with different outputs, equipment sets, and location growth paths. Also, the early phases are in already developed areas and can evolve in place using conventional equipment as a starting point. Locations in later phases are more undeveloped, uninhabited, and have difficult or hostile conditions. So new locations must start out with more complete equipment sets (seeds) that are imported from elsewhere. More of the work at first will be by temporary workers or remote and automated operation, until suitable habitation is set up for permanent occupancy. Another reason for design phases is to apply the experience gained in the earlier ones to the more difficult tasks of the later ones.
- New phases begin whenever the first elements for that design phase are produced and start to operate. A location which reached some level of maturity in the previous phase can continue to operate, using equipment it already has. The later phase can operate in parallel at the same location, and gradually replace or upgrade previous equipment.
- Phase 0 - Research and Development outputs final designs for the later phases to implement. These are open-source, in order to encourage widespread use. R&D may occur at many locations, with varying levels of participation. Individuals and groups are encouraged to communicate and collaborate. Since it is the first project phase, it cannot evolve from previous ones. Instead it must start with conventional buildings, tools, machines, design methods, and skills. It can develop new methods and technologies to use for itself in the course of working towards later phase designs. It may produce some products for sale, to help fund more R&D, and as a consequence of testing prototype equipment, and it may also use any production outputs internally to help expand and upgrade the R&D equipment. Final designs should have a long operating life, so prototypes built and tested before making the designs final will likely last longer than needed to test. Therefore prototypes can also be sold, or delivered to other locations or later phases to use. Lastly, the R&D phase may produce final versions of elements for starter sets (seeds). These starter sets are then used to establish new locations.
- Phase 1 - Starter Locations and Network may start with conventional tools and equipment, but would gradually upgrade as final designs become available. Later locations have the benefit of more designs being available, and can therefore build or acquire more complete starter sets right away. Once multiple locations exist, they can network with each other to collaborate on projects and trade with each other. Equipment for this phase is designed for personal scale hobby and home use. Their duty cycle (percentage of time in operation) is less than full time, and items are smaller and less expensive. Individuals or small groups can afford a number of these smaller items, and house them in space they already have or can build or rent without too much difficulty. Like all parts of the project, people's skills and the equipment they work with are not intended to reach a static end point. Individual nodes may not grow, but the network as a whole is intended to gradually add more prototypes and new final designs, copy existing items, and scale them to larger (and sometimes smaller) sizes. As the network upgrades itself, it can produce more items internally for further upgrades, and more end products for members to use.
- Phase 2A - Distributed Locations: Eventually the accumulation and scaling of equipment in Phase 1 leads some members to move beyond hobby and home use, towards small business and commercial operation. This is characterized by part or full time operation, and selling products outside the network. The larger scale and higher duty cycle will require new designs optimized for those purposes. Phase 1 equipment was optimized more for flexibility than speed. That way a smaller number of items could do more tasks, and lower initial costs. When running a business, speed and efficiency become more important, so the designs are optimized to do particular tasks well. This results in a larger collection of more specialized items. Skills and training also become more specialized and take longer to learn. Particular nodes will tend to become more specialized and trade for other things they need, although a comprehensive large location that does most things is still possible.
- Phase 2B - Industrial Locations are in the same kind of developed areas and temperate climate as Phase 2A Distributed Locations, so we group them together in Phase 2. Industrial locations can evolve from distributed small business or commercial nodes by increasing scale and more specialization. They can also be built as fresh locations. In that case, the larger equipment and space to house them will likely need outside capital, because individuals or a small group won't have enough funds. Gradual evolution from a smaller size by self-production would not require as much, or any, funding. Providing larger work spaces and meeting input and output needs will tend to limit industrial locations to fewer products. For example, if you are processing scrap metal on an industrial scale into new metal stock, it helps to be near a rail line to deliver the scrap and deliver the finished products. The more products, factory space, and specialized needs you have, the less likely you will find one big location that can satisfy all of them.
- Industrial scale production is sold to a wide range of customers beyond a single metropolitan area or short travel distance. Suitable transport capacity becomes more important. A narrow product range and large scale markets means demand can be more variable. Distributed finance and ownership makes sense in this circumstance. Demand may be low for a particular product, but may be high for something else. In a distributed portfolio these tend to average out. Owners can then reassign their labor and equipment as needed to meet the higher demand products. Given a high capacity to recycle and self-produce, modifying equipment is easier to do.
2.3.1.2 - Design Studies
[edit | edit source]This section identifies design studies to be done and methods to carry them out. The actual design work is recorded in 3.0 Hardware Design and 4.0 Software Design and later sections.
Design of Starter Sets
[edit | edit source]Starter sets are a key part of the seed factory concept, so how they are designed is an important question. Our current approach is as follows:
- (1) Identify the desired mature state for the production network by phase, location, and top level functions. The mature state can be described in terms of output flows between functions, and to other locations, phases, and other parts of civilization. The organization of ownership and control is not as important as the products and services being supplied. Output flows can be organized into a product breakdown structure according to internal functional analysis and classifications of industries such as the NAICS.
- (1a) We don't have the time or staff to account for every kind of output a production network may make. Since our goal here is to find generally useful starter sets, we will sample popular or typical products. Other people can then modify or add to those sets as needed. For phases in general we suggest using popular products from a sampling of industry categories as examples. For early phases we suggest using common small-scale hobby, residential, or commercial products.
- (2) Break down top level functions by their estimated needs for materials, processes, labor, energy, working space, etc. to produce the outputs and products for step 1. Develop a flow diagram according to the reference architecture in section 2.3.1.5.
- (3) Identify the equipment needed to meet the requirements in step 2. Configure the equipment, floor space, buildings, and locations into logical factory plans and network flows. From this, identify transport needs between elements.
- (4) Formulate logical growth sequences to reach the equipment in 3. Growth steps are identified in terms of scale and product range, and which functions are performed internally vs outside supply. One logical path is to work backwards from the final products, and add more steps towards raw inputs. Another is starting small but performing all the steps, and mainly scaling in size. A third is starting with a few key products, and adding more over time. Other growth paths or combinations of the three listed are also possible.
- (5) Sequence the equipment and input resources needed to accomplish the growth sequence. Some machines come earlier because they are more general purpose or required to make other machines needed later. Others may have priority because they provide larger cost savings or gains in output range.
- (6) Trade alternatives and optimize sizing in steps 3 to 5 to reach preferred designs for the starter set. Alternatives include processes, machine types, sizes, and sequence. Because many growth paths and many machines are possible, automated path simulation and variation would be useful.
- (7) Identify the optimal starter set to begin the sequence. Consider what is available from previous phases or inputs from civilization at large. Also consider the ability to grow in range of outputs, scaling, and growth rate. Also consider number of machines in the starter set. Too few machines may not have enough ability to bootstrap growth, while too many increases starting cost and complexity.
Besides selecting starter sets, outputs of this task include the other input flows to start a phase or location. A starter set of machines may be supplied ready-to-use, or built from parts and materials. In that case you need those parts and materials as inputs. The starter set by itself is not all you need to operate a factory. You will need people with suitable skills, conventional tools and accessories, raw materials and parts, land use rights for a location (i.e. purchase or lease), etc. Outputs from this task also include research and development needs for desired technology not yet available, and needs for specific designs of items for the starter sets and expansion sets to reach maturity. These needs are passed back to the appropriate parts of Phase 0 - Research and Development.
2.3.1.5 - System Architecture
[edit | edit source]Reference Architecture Purpose
[edit | edit source]
Our project contains multiple phases and locations, and they interact with the rest of civilization. We adopt a Reference Architecture approach to simplify the design work. This architecture captures the shared elements within different phases and locations. These elements can then be related to each other, and shared design elements used multiple times. It also relates project elements to civilization as a whole. For example, a given location will likely use electrical power, as does the phase as a whole. The developed parts of civilization which interact with the location can supply and receive power from it. The "Provide Power" part of the reference architecture addresses all of these. If we are producing our own electrical parts, then we can standardize their design, and make them compatible with parts supplied from outside the project.
A reference architecture can also be used for analysis, modeling, and trade studies using shared processes and data formats. Different design options, locations, or phases will generate different data values. With a shared architecture they can be more easily compared and summarized. A given location or phase will have some unique elements, so we don't apply the reference architecture as a rigid template. But if, say, 80% of a design is shared across multiple phases and locations, that is still a substantial savings over doing a unique design for every case.
Architecture Derivation
[edit | edit source]
Self-expanding systems always include a growth period. They may or may not have a period of stable operations after reaching a desired mature state. A growing system will generally interact with and depend on existing industries for the things it can't do yet. At a minimum it will get a starter set of equipment, and likely additional materials, parts, and equipment during growth. It is possible an expanded system can become completely independent, but we don't expect this to happen until later phases. This is because some rare materials, hard to make items, or specialize services remain better supplied from outside. Our reference architecture should then cover these parts of civilization outside the project.
The major goal of our work is upgrading and expanding civilization, and solving some of the problems it has. So our reference architecture should also cover other aspects of current civilization to allow comparing existing with new designs and identifying input and output flows. We can use the list of existing industry categories in Appendix A.1 as a source for this. Building a new location in an undeveloped area is similar to the building of civilizations and colonies in the past, so reviewing their history can provide some guidance on what to include. Finally, as our work progresses, we may identify new elements to include in our architecture.
Previous Work
[edit | edit source]
Top level functions for the architecture were previously derived from early studies and analysis of the seed factory concept. This work is reported in Section 9 - Conceptual Design Notes of the Seed Factories book. The four top functions we initially identified are Production, Habitation, Transport, and Services. These were then divided into lower tier functions as follows:
Production
[edit | edit source]The production function is mainly organized in order of production processes:
- Control Systems - This function collects data and issues commands to other parts of a location. It uses operator inputs and communications networks.
- Supply Power - This function collects energy from the environment plus utility and delivered energy supplies like fuels. It supplies the power to other production functions and the other top level functions.
- Extract Raw Materials - This function takes land, water, and air resources, plus mining equipment and energy, to extract raw materials from the environment. The raw materials are generally processed further.
- Process Materials - This function takes raw and recyclable materials and converts them into ready inventories. Ready materials can be used directly, such as lumber for construction, or used for further production, like basic metal shapes. Processing uses specialized equipment and energy.
- Fabricate Parts - This function takes ready materials like wood or metal, and converts them to finished parts.
- Store Inventory - This function provides space to keep equipment not currently being used, materials and parts between operations, and final products awaiting delivery.
- Assemble Products - This function takes internally made parts and ready materials, plus outside supplies, and turns them into completed products. Some of those products are used for maintenance and expansion of other functions.
- Grow Organics - This is a separate function because living things do most of the above production steps internally, and you can't turn off living things the way you can a machine tool.
Habitation
[edit | edit source]Habitation includes living and working space for humans, and non-productive living things like pets and ornamental plants. Habitation includes both indoor and outdoor spaces, and private, community, public, and commercial spaces. Restrooms and break room/snack areas in a factory building are habitation elements, because they are only there because people are there. A roof and climate control for a factory, that is primarily to protect production equipment, is a production element. The functions that make up habitation include:
- Protect from External Environments - This includes land, foundations, structural frames, moisture protection, wind, insects, thermal insulation, and protective (as opposed to decorative) clothing. Beyond Earth, it would include protection from radiation, vacuum, and lack of gravity.
- Control of Internal Environments - This includes electrical power, temperature and humidity control, natural and artificial lighting, and acoustics (both damping and artificial sound)
- Provide Food and Drink - This includes supply of food, drink, and potable water, and kitchen and dining equipment to prepare and serve these items. Growing food is under Production/Grow Organics.
- Maintain Health - These are the basic functions humans need to sustain themselves besides food and drink: sleep, sanitation, exercise, body cleaning, environmental cleaning and filtering, health monitoring, first aid, examination, and treatment.
- Provide Personal Items - This includes personal living space and storage, community space: meeting, dining, recreational, office, and retail; furniture and decorations, and decorative clothing.
- Provide Information - This covers everything from printed books, to audio, video, internet, and portable electronics. There is no particular distinction between personal and business equipment. High level/remote operation of Production/Control Systems may use the same equipment. Internal/local sensors and networking may be particular to the production elements.
Transport
[edit | edit source]Transport functions were initially organized according to the type of item being transported, to line up with the types of input and output flows at the project, phase, or location level:
- Transport Energy - This includes electrical power, fuel, and other energy types.
- Transport Food - This includes refrigerated, dry, canned, and finished food types. It also includes transporting unprocessed foods like raw grains and livestock.
- Transport Water - This includes potable water in pipes, tanks, and small containers. Wells are part of Production/Extract Materials, and storm drainage is part of Habitation/Protect from External Environment.
- Transport Parts and Materials - These can be in bulk form, such as a load of gravel or lumber, or packaged items.
- Transport Tools and Machines - These include portable tools which can be hand-carried, larger tools and machines which are transported to work sites, and stationary tools and machines delivered to a production location.
- Transport Land and Asset Rights - For land, this is moving the rights, not the land itself. For other assets they may or may not be moved physically. Rights may be transported by paper or electronic documents.
- Transport People and Services - This includes passengers, personal self-transport, and transporting people to work sites, as distinct from transporting equipment. The safety requirements for people are higher, and automated equipment vehicles may drive themselves, thus making distinct functions.
- Transport Funding and Obligations - This includes items like financial payments and contracts. These can also be transported in paper or electronic forms.
- Transport Information - This includes all types of information that are not rights, funding, or obligations. It can be voice, video, images, text, paper, and other formats.
- Transport Wastes - In this context, wastes are relative to a given function. They may be recycled or used as inputs elsewhere. Types of waste include scrap (leftover or old materials that can be recycled, trash (unrecyclable or burnable items), garbage (food waste and other compostable items), junk (non-functioning items from which parts and materials may be salvaged). It also includes items not usable in their current form like solid, liquid, airborne, chemical, and thermal wastes. They may be transported elsewhere to be cleaned or recycled.
These were later grouped into a six functions by type of item being transported:
- Transport Energy - this is conventionally distributed by electric and other utilities.
- Transport Discrete Cargo - this covers food, parts, materials, tools, machines, and wastes that require environmental/handling protection, and completed products for delivery.
- Transport Bulk Cargo - this includes items which do not require special handling or protection, but merely carriage from place to place. Examples include raw materials like crushed stone, and bulk wastes.
- Transport Fluids and Gases - this includes delivery by pipes and tanks, such as water, natural gas, and propane.
- Transport Humans - This type of transport adds habitation elements for comfort and increased safety compared to basic transport for inanimate cargo. Some delicate cargo may be carried by the same systems used for people. An example is luggage and air cargo carried by passenger aircraft.
- Transport Data - This includes in particular legal rights and money, but also a vast array and quantity of other information. Traditionally data was transported in paper form, but now is mostly by electronic networks and storage.
Services
[edit | edit source]Services were not analyzed in detail in previous studies, but we can state a few things about them:
Supporting services can be performed internally to other functions. For example, the Store Inventory part of Production may be performed internally, or supplied by outside storage services. Many people prepare their own food and drink at home, which would be internal to Habitation, while from outside they can be supplied by a variety of dining services. Generally outside services are more specialized or efficient in some way. They can then be chosen even if they are able to be done internally.
There are too many service types to list them here individually, but categories include markets, rental, engineering and design, finance, insurance, medical, legal, business support, education, social assistance, arts and recreation, dining and lodging, and private and public organizations. Providing services generally requires people with specialized knowledge, and items from Production, Habitation, Transport, or other Services to carry out. They may provide end-point consumption to satisfy people's needs and wants, where their outputs are not used in further economic activity. Alternately the services may be integrated with internal system functions and flows as part of their operations.
Industry Analysis
[edit | edit source]
We want to identify any additional functions that should be added to the reference architecture. One method is to compare the list of all industry categories in Appendix A.1 to our existing architecture version. This list is a summary of the 2012 NAICS developed by the US Census Bureau for statistical purposes (it has since been updated to the 2017 version). The following table correlates our architecture structure to the industry categories:
1.0 Provide Production Capacity
- 1.1 Control Location
- 1.1.1 Control External Flows
- 1.1.2 Control Location Production
- 1.1.3 Control Location Habitation
- 1.1.4 Control Location Transport
- 1.1.5 Plan Location Operations
- 1.1.6 Analyze Location Performance
- 1.2 Supply Power
- 1.2.1 Supply External Power
- 1.2.2 Supply Location Power
- 1.2.3 Supply Temporary Power
- 1.3 Extract Materials
- 1.3.1 Extract Minerals - 212 Mining, 213 Mining Support
- 1.3.2 Extract Organics - 114 Fishing Hunting & Trapping
- 1.3.3 Extract Fluids and Gases - 211 Oil & Gas
- 1.3.4 Extract Wastes - 5629 Other Waste Services
- 1.4 Process Materials
- 311 Food Manufacturing, 312 Beverage and Plant Extracts
- 313 Textiles, 3161 Leather & Hide Tanning & Finishing
- 3211 Sawmills & Wood Preservation
- 322 Paper Products
- 324 Petroleum & Coal
- 325 Chemicals
- 331 Primary Metals
- 5622 Waste Treatment & Disposal
- 1.4.1 Physical Processing
- 1.4.2 Electromagnetic Processing
- 1.4.3 Chemical Processing
- 1.5 Fabricate Parts
- 1.5.0 Maintain Safety and Shop Equipment
- 1.5.1 Use Hand & Portable Tools
- 1.5.2 Use Stone & Concrete Tools - 3271 Clay & Refractories, 3273 Cement & Concrete, 3274 Lime & Gypsum, 3279 - Other Mineral Products
- 1.5.3 Use Metalworking Tools - 332 Fabricated Metals
- 1.5.4 Use Woodworking Tools - 3212 Veneer Plywood & Engineered Wood
- 1.5.5 Use Glass & Ceramics Tools - 3272 Glass
- 1.5.6 Use Polymer Tools - 326 Plastic & Rubber Products
- 1.5.7 Use Electrical & Electronics Tools - 3344 Semiconductors & Electronics
- 1.5.8 Use Coatings & Printing Tools - 323 Printing & Related
- 1.5.9 Use Fiber & Fabric Tools - 314 Textile Products
- 1.5.10 Use Light Craft Tools
- 1.6 Store Inventory
- 1.6.1 Provide Outdoor Storage (includes partial shelters)
- 1.6.2 Provide Enclosed Buildings (includes conditioned & specialty storage) - 493 Warehousing & Storage
- 1.6.3 Provide Storage Equipment
- 1.6.4 Store Materials Inventory
- 1.6.5 Store Parts Inventory
- 1.6.6 Store Product Inventory
- 1.6.7 Store Tools & Equipment
- 1.7 Assemble Elements
- 333 Machinery Design & Manufacturing
- 334 Computer & Electronic Products (except 3344)
- 335 Electrical Equipment
- 336 Transport Equipment
- 337 Furniture Products
- 339 Miscellaneous Manufacturing
- 811 Repair & Maintenance Services
- 1.7.1 Fasten Mechanical Items - 315 Apparel, 3162 Footwear, 3169 Leather & Related Goods, 3219 Other Wood Products
- 1.7.2 Fuse and Weld Items
- 1.7.3 Assemble with Adhesives
- 1.7.4 Perform Outdoor Construction - 237 Heavy Construction & Civil Engineering
- 1.7.5 Perform Indoor Construction - 236 Construction of Buildings, 238 Specialty Construction Trades
- 1.8 Grow Organics
- 1.8.1 Grow Forest Products - 113 Forestry
- 1.8.2 Grow Agricultural Products - 111 Farming, 112 Animals & Aquaculture, 115 Agriculture Support
- 1.8.3 Grow Biotechnical Products
2.0 Provide Habitation Capacity - 814 Private Households
- 2.1 Protect from External Environment
- 2.1.1 Supply & Maintain Land
- 2.1.2 Supply & Maintain Buildings - 5617 Building Services, 721 Accommodations
- 2.2 Control Internal Environment
- 2.3 Provide Food and Drink - 722 Food & Drink
- 2.4 Maintain Health - 621 Ambulatory Health Care, 622 Hospitals, 623 Nursing & Residential Care, 812 Personal & Laundry Services
- 2.5 Provide Personal Items
- 2.6 Provide Information
3.0 Provide Transport Capacity
- 3.1 Provide Transport Infrastructure - 488 Transport Support
- 3.2 Transport Bulk Cargo - 482 Rail Transport, 483 Water Transport, 5621 Waste Collection
- 3.3 Transport Discrete Cargo
- 3.3.1 Supply Cargo Vehicles
- 3.3.2 Supply Cargo Equipment
- 3.3.3 Supply Cargo Containers
- 3.3.4 Operate Cargo Transport - 484 Truck Transport, 491 Mail Transport, 492 Couriers & Messengers
- 3.4 Transport Humans
- 3.4.1 Supply Passenger Vehicles
- 3.4.2 Operate Passenger Vehicles - 481 Air Transport, 485 Transit & Ground Passengers, 487 Scenic & Sightseeing Transport
- 3.5 Transport Energy - 2211 Electric Power
- 3.6 Transport Fluids and Gases - 2212 Natural Gas, 2213 Water Sewage Other, 486 Pipelines
- 3.7 Transport Data - 515 Broadcasting, 517 Telecommunications
4.0 Provide Supporting Services
- 4.1 Supply Trade Services - 42 Wholesale Trade, 44-45 Retail Trade
- 4.2 Supply Information Services - 511 Publishing, 512 Video & Audio Production, 518 Data Services, 519 Other Information
- 4.3 Supply Financial Services - 52 Finance & Insurance
- 4.4 Supply Property Services - 53 Real Estate Rental & Leases
- 4.5 Supply Specialized Services - 54 Professional Scientific & Technical
- 4.6 Supply Education Services - 61 Educational Services, 712 History
- 4.7 Supply Social Services - 624 Social Assistance
- 4.8 Supply Entertainment Services - 711 Performing Arts & Sports, 713 Recreation
- 4.9 Supply Organization Services - 813 Organizations, 92 Public Administration, 551 Management, 561 Administration (except 5617)
Historical Analysis
[edit | edit source]
[Material to Be Moved Elsewhere]
[edit | edit source]Functional Flows
[edit | edit source]Functions are logically connected by flows that go between them, or which enter and leave a system, location, phase, the project, or civilization as a whole. For civilization, sunlight and heat radiated to space are examples which enter and leave from outside. All flows must be accounted for in a complete system model or design. They must have identified starting and end points, even if those are outside the system being considered. Flows are not changed between end points, that only happens inside functions. Flows may split and merge, but their quantities must add up to the same total before and after. Otherwise you have creation or destruction which is unaccounted for. Flows do not have to represent physical movement. They may be a time sequence, such as "airplane at gate", "airplane on taxiway", "airplane on runway", "airplane in flight". In that case, the airplane in a given condition is the output of one function and the input to the next, without a change in between.
Factory Organization
[edit | edit source]Historically a "factory" brought people and equipment together in one place. The limits on power sources, transportation, and communications made a single location a more efficient way to coordinate the production steps. Today we don't have to rely on a central steam engine with pulleys and shafts, or a river with a water wheel to supply power. Electricity can be distributed to wherever we need it. Modern transportation is up to a thousand times more productive in terms of momentum per person when compared to pre-industrial methods. Lastly, high speed communications allow people to work remotely and equipment to be networked.
Therefore production can be distributed in multiple locations, and still be coordinated. It is not required to be spread out, though. There are still good reasons to keep some production steps together in one place. We therefore have a new concept of a factory as organizing the factors of production under for a shared purpose, whatever the method of ownership and physical locations. That purpose can include self-consumption by the owners, sale or distribution to others, self-expansion of the factory, or a combination. This concept allows us to design the production flows according to what works best, without forcing it all to be centralized in one place.
Production flows that follow individual design instructions and production orders can produce a variety of products. This is in contrast to dedicated equipment that can only do a specific task. We can thus organize a "general purpose factory" with a variety of equipment that can perform different tasks, and be linked in different production paths to make a wide variety of products. General purpose factories can be measured by scale from personal, to commercial, to industrial. They can also be measured by maturity, from a starter set, through various growth stages until it reaches a desired scale and output range. Finally, they can be measured by closure, what percentage of items for expansion and maintenance it can produce internally.
Since general purpose factories are by their nature flexible, their growth paths and mature state may not be defined in advance. They can change course according to individual or market needs. A specialized factory optimized for specific products requires knowing what those products are from the start. On the other hand, a specialized factory is typically simpler, needing fewer pieces of equipment and following fixed production flows.