The Seed Factory Project
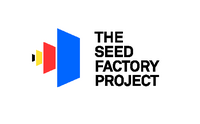
- 2.3.2 Project Design Studies
2.3.2.9 - Archived Studies
[edit | edit source]
Archived studies are now out of date, but saved for reference. The first such archived study is a conceptual design for a Community Factory:
A. - Community Factory [Archived]
[edit | edit source]
This section (5.0 and the following pages) and the notes in section 9.0 comprise an extensive example in how to start a Seed Factory design. It is an "example by doing" of an actual proposed project, and not just a theoretical textbook example. It follows the design concepts and process described earlier in the book to start developing a Community Factory. The Conceptual Design developed here is the first stage of a design project. That stage starts with a general set of needs and goals and ends with a complete system concept. That concept identifies the major parts of the system, their general size, configuration, and technology, and how the system would be operated and maintained. The objective in this design stage is to demonstrate overall feasibility of the project, and the ability to meet the intended design requirements. Following this stage would be preliminary and then detailed design. The latter ends with design files ready for production. The design is incomplete at present, so the details in the book only represent what has been done so far.
A.1 - Concept Summary
[edit | edit source]We start with a summary of the purpose and main features of the Community Factory. The following pages and sections then follow the steps in the design process.
- Purpose - The Community Factory is intended to deliver most of the basic food, shelter, and utility needs for an owner/operator community of 660 people in the vicinity of Atlanta, GA. The "Community" in the project name refers to it serving a local community, and that most of the outputs go directly to the owners. The factory design is likely to be too big and complicated to be built and operated by one person, and therefore needs multiple owners. Various ownership methods are possible. The factory as a whole may be owned by all the community members as a cooperative or by shares. Alternately, parts of the factory may be owned by individuals or groups, who coordinate the operation as a whole. Reasons for people to build and operate such an automated factory include that it can supply their needs cheaper and with less labor than conventional methods, and as owners they are more secure in their position compared to employees. Additional reasons are potentially faster growth rates than other investments, and a better quality of life. For the purpose of our example, we specify a particular size and location for the Factory because many of the design details depend on knowing them. If another size or location were chosen, those details would would be different. The community is assumed to be located within reasonable travel distance (a few hours), with a concentration around a main location. Some people may participate remotely from larger distances, but on-site operation of the Factory and delivery of the outputs is easier over short distances.
- Rationale - Why we consider this as a design example is distinct from the reasons future owners would have to build it. The Earth will need to support several billion more people by mid-century, and everyone, not just the added population, would like a decent quality of life. For such goals to be sustainable, communities need to operate mostly from local materials and energy resources with high levels of recycling, and be less dependent on consuming scarce resources with exhaustible supplies. A project that supports a local community should be of manageable size and complexity, and if successful can be duplicated as many times as needed to meet larger goals. Our other examples will explore different applications: larger scale industrial, more distributed without a main location, and more difficult and remote locations.
- Evolution - The Factory evolves over a period of years from a partly automated starter set, or "Seed Factory". The starter set is built and operated by an original community, using conventional tools and equipment (Figure 5.0-1). The conventional workshop plus the first set of automated equipment form the seed. The original community would live and work in conventional homes and jobs, and begin work on the project part-time. As the Factory capacity expands, it produces more outputs, and needs more people to operate it. So some community members will transition to working full time on the project, and new members will join the community.
- The starter set plus conventional equipment is used to make growth equipment in a series of expansion phases. This includes more copies of existing equipment, larger versions for increased scale and output, and new and different equipment to handle other processes. Throughout the growth process, outside supplies of parts and materials are needed for whatever items the Factory cannot make internally. As the Factory matures over time, the percentage of outside supplies should decrease. Surplus products above what the owners use for themselves are sold to pay for outside supplies for the Factory, and for income to the owners.
- Since self-expanding factories are a new idea, a research and development phase is needed before the first operating Seed Factory elements are built. This phase includes developing new ideas and design approaches, documenting them in a form other people can use (such as this book), testing component technologies, factory element design, and building and testing prototypes. We expect the early part of this work is by way of a distributed open source collaboration. More work will be needed for growth items and improvements, so the research and development phase will continue in parallel with building and operating the growing factory.
- When the factory reaches the design capacity of 660 people, the owners can decide to stay at that level, work on upgrades to the equipment, further growth of the community, or to seed a new community in a new location. These would constitute a new project stage, which is beyond the scope of the current project design.
- Organization - The Factory is set up as one or more private projects, such as Limited Liability Corporations or Owners Associations. The various projects make agreements to supply each other, coordinate operations, and settle payments as needed so that the Community Factory as a whole functions effectively. Project members get proportional ownership and use of their project, and the products and sales income it generates, according to their net contributions. New contributions consist of design work, money, tools, materials, and labor for the original construction or continuing operation of the Factory. Owners can choose to draw fewer products or income than their share entitles them to, the difference adding to their total share. They can also choose to draw out more than their share, or sell their share to someone else, but the timing and details of excess draws may be limited for practical reasons. Excess draws or sale would reduce their share of the project. Decision making would be mostly proportional to ownership share. Some additional decision weight is allowed for people living and working at the project location, since they are more affected by such decisions than non-local owners.
- Land - The project requires land for a number of purposes. Figure 5.0-2 shows the relative land areas as if it were one rectangular land parcel. Most likely it will actually be arranged in separate and more irregular parcels, which are acquired as needed. Total project land, including the industrial, residential and commercial areas is estimated at 4500 m2/person or just under 300 hectares (740 acres). The land area for each person is estimated to include 1000 m2 for residential and commercial, including 200 m2 of building floor area, 500 m2 for industrial land, of which 200 m2 is buildings or constructed equipment, 500 m2 for farm and greenhouse space, and 2500 m2 for sustaining forest and raw materials extraction. During initial construction some extra land or sources of materials may be needed. The land is assumed to be undeveloped at first, and built up in the course of the project. We expect that most of the land will be purchased, but at the early stages some leased industrial land may be used, and mining and timber rights may be used as an alternate to outright purchase. A main location allows better integration of automation between factory steps, for the owner/operators who live there to have short distances for daily travel, and for easy return of materials for recycling. However we expect some people will want to live at separate locations by personal preference.
- Energy - The project also requires a significant amount of energy to operate the Factory, and to supply to the residential and commercial areas. The main location includes its own equipment for producing the power and distributing it locally. If it is too inefficient to build small power units for people living at separate locations, then the main location would generate a surplus and sell it, and use that income to pay for distributed energy delivery by local utilities. For the energy production to be sustainable, the main sources are assumed to include types like solar, wind, and biofuels. Since these sources are variable, a combination of local storage and connection to outside utilities will be used to level out supply vs demand.
A.2 - Study Sections
[edit | edit source]The details for this design example are organized into the following sections:
- 5.1 - Requirements - The general goals of the project are converted to more detailed and specific system requirements for the design to meet, and a scoring system to evaluate the resulting designs.
- 5.2 - Functions - The overall project is divided into smaller parts, and flows connecting the parts, which when combined will meet the intended goals.
A.3 - System Requirements
[edit | edit source]This section lists the initial set of system requirements for the Personal Factory project. It is the first step in the Systems Engineering process described in Section 4.0. It puts into measurable and specific terms what we want the Factory to do. They are organized into categories, and numbered for later reference. The requirements are written in terms of the Mature Factory when it has reached full capacity. The Seed Factory design, which will be the starting point for growth, is determined later in the design process from what is needed to reach that final capacity.
Following the text of each requirement we discuss how they were arrived at, but there is no "right answer" to setting requirements, they are a matter of the end user's goals and choices. In fact, this particular set of requirements was derived from a larger goal of improving the quality of life for an expanding civilization. Parts of that larger goal will be addressed in the other design examples, but they only affect the Personal Factory as far as providing a source for the requirements below. Just because we want the factory to meet these requirements is no guarantee they are possible or economically feasible. This is why we call them the initial set of requirements. As the design progresses they will most likely need adjustment to what is practical or help identify areas that require more development.
1. Objectives
- 1.1 Project Goal - The project shall provide a locally owned and operated Personal Factory System which supports the physical needs of the owners.
This sets the operating regime and basic design function that the system will perform. It is a binary (Yes/No or True/False) type requirement. The requirement is either met or not met. Locally broadly means "within several hours travel time", or approximately a metropolitan area and surroundings. This will be made more explicit later.
- 1.2 Project Scale - The system shall support 75 people the first year, and 75 additional people/year until a full capacity of 660 people.
A target size is needed so you can work towards definite designs. The particular goal of 660 people is somewhat arbitrary, but is based on historical examples of settling new communities. The idea is that 660 people would have enough different skills to operate the various parts of the factory. If later design work shows this number is either too small, or larger than necessary, it can be changed. But we need starting values for numerical requirements for the first cycle of design.
- 1.3 Choice - The specific physical locations for the project, and their internal organization, function, and operation shall be chosen by program participants and location residents within the limits of design constraints.
The intent of this requirement is that the owner-operators of the factory will choose where it is built and how it is operated, rather than these decisions being made from the outside. Completed designs for the factory elements gives them a starting point to work from, but the final choices will be theirs.
2. Performance
- 2.1 Location - The system shall be designed to operate in a temperate environment, as defined by the middle 90% of world population.
We want it to operate under the range of conditions where the majority of people actually live. The outer 5% on each end of the environment range are left out for this first-generation design. Setting a range establishes definite design limits. Later versions may be adapted to more difficult conditions.
- 2.2 Growth - The system shall be able to increase capacity for production, transport, and habitation by 11% per year after initial start-up.
To make the design desirable for the owners, it should be able to more than just maintain itself, and have a generous margin for growth. The extra capacity could be used to increase the community size, start up new locations, or make products for sale. Initial start-up refers growth phases before supporting 75 people the first year, when the system is expanding from starter set to mature capacity.
- 2.3 Improved Technology - The system shall increase the levels of self-production, cyclic flows, and autonomy in a progressive manner.
We do not expect the starter set to have the same abilities as a mature system supporting 660 people. This requirement sets a gradual increase in technical performance as the factory grows. To put it in more concrete terms, we divide this requirement into more detailed ones. The final level is set to 85% for the various detailed requirements as a reasonable goal for a first-generation design.
- 2.3.1 Local Resources - Provide 85% of continuing matter and energy needs from local resources, as measured by economic value.
This meets the design goal of "supports most of the physical needs". 85% is for a mature factory. The remaining 15% would include rare or hard-to-make items which would be difficult for a small-scale local factory. We expect the parent requirement of progressive improvement would be met at a decreasing rate vs size. The easiest items that contribute most to the 85% goal will likely be added first to the factory.
- 2.3.2 Self Production - Provide 85% of the total economic value for the owners internally, with the remainder from outside work.
The previous requirement covers physical needs, this one is economic value which the factory generates, including work by the owners as operators. Again, we think 85% is a reasonable level for a mature system, with a gradual increase as the factory grows. The remaining 15% would be conventional outside work elsewhere. A corollary of this requirement is that the early stages from the starter set would only support part-time operation or a few full-time people, while meeting only some local needs. Most participants would be doing conventional outside work at that point. We think a gradual shift as each person individually transitions from outside work is more feasible than doing so all at once.
- 2.3.3 Cyclic Flows - The system shall recycle and reprocess 85% by mass of local waste flows from production, transport, and habitation.
This requirement comes from several sources. Closed cycle flows are more sustainable in the long term. They have lower input costs because you do not need as many new inputs. They also have lower disposal costs than linear flows produce. We expect that the factory's ability to work from raw materials and level of automation will make the recycling economically inexpensive. The 85% goal is again for the mature factory.
- 2.3.4 Automation - The system shall reduce human labor requirements by 85% relative to the US average.
Automation is desirable from a quality of life standpoint - more output for less work. The factory owners do not have to worry about automation putting themselves out of jobs, since they own the production. Less work and economic security are key parts of making the Personal Factory something people will want. We think 85% automation is a reasonable level for a first generation mature factory. It assumes the factory as a whole is integrated, so that transfers between production steps can be automated, as well as the individual steps.
- 2.3.5 Autonomy - The system shall be capable of controlling at least 85% of production, operations, and maintenance functions locally.
This flows partly from the desire for owner choice and ability to run things under control of the people who live with the results. Having the capability does not require it be used. Participants or specialists who are not in the local area can operate parts of the factory by remote control as an option.
- 2.3.6 Complexity - The starter set shall include not more than 7 major production elements, not counting attachments.
One of the growth paths for the Personal Factory is diversifying to new equipment and processes out of the hundreds of types available. We wish to start with a reduced set to lower initial cost and design complexity. On the other hand we do not want to start with too little. For example, we could in theory start with zero production elements and rebuild technology starting from rocks, sticks and fire made by hand, but that is not very practical. A compromise is to start with about one piece of equipment per major production function, so that a reasonably complete production chain is possible within the factory. Attachments, bits, consumable supplies, tooling, and small shop tools will be needed to outfit any operating factory, but are not counted as major elements.
- 2.4 Improved Quality of Life - The system shall support an equivalent GDP/person of $156,000 referenced to January 2013.
The goal of supporting physical needs does not say at what level of quality for food, shelter, and utilities. Naturally we would like a high level of quality, and we think with automation and self-production this can be reached. The GDP equivalence sets a target well above the US average, and is in terms of what it would cost to reproduce the lifestyle and income in 2013 dollars. Cash income will be much less, since most items will be supplied directly from the factory. As with other requirements, this is a goal for the mature factory, early versions will not reach this high.
- 2.5 Data - The system shall share project experience and data with the local community and beyond.
As a first of it's kind project, we would like others to build on the knowledge gained and hopefully feed back their own experience. Including it as a system requirement ensures a process for collecting and then sharing the data will be included in the design. We recognize that personal data will need to be carefully protected. This requirement is about technical features like solar collector power output.
- 2.6 Resources - The system shall produce at least 10.5 times internal needs for materials and energy.
This comes from a desire for a highly productive design that comfortably produces above it's own maintenance and support needs. It also supports a high quality of life either by directly supplying items to the owners, growth of the factory, or surplus production for sale. This is measured for the mature factory, after building facilities and equipment, and community residences have reached 660 capacity. It is related to the concept of "energy return on energy invested" (EROEI) for energy sources, but extended to also cover material resources.
3. Time
- 3.1 Completion Time - [Not Applicable]
A project schedule or completion date is often used as a time-based requirement. In this set of requirements it is already implicit under 1.2 Project Scale as 660 person final size/(75 people/year growth) = 9 years from start of full construction to completion. We mark 3.1 Completion Time as "Not Applicable", at the system level, since we try not to have duplicate requirements. At more detailed levels of the project, we may set time and schedule requirements, and reserve this requirement number (3.1) for that purpose.
- 3.2 Operating Life - The system will be designed for an indefinite life with maintenance, repair, and replacement of parts.
This project is intended as a permanent source to supply the owner's needs. Therefore it will not have a finite life or wear out date. Since the individual elements cannot be designed to last forever, a consequence of this requirement is the need for maintenance and repair tasks.
4. Cost
- 4.1 Total Development Cost - Development cost for the project shall be less than $66 million for a capacity of 75 people per year, net of sales.
We use January 2013 US dollars, adjusted for inflation. Cost requirements put a bound on how much effort goes into designing and building the system. Total costs are divided into Development - the one-time costs for technology, prototypes, and design; and Location - the repeating costs for each added unit or copy you build. The agricultural, construction, and utility industries, which our factory outputs fall within, typically do not invest a lot in research and development. Since we want to apply modern automation to these areas, we assume a relatively high development cost. The specific number is a multiple of the expected unit cost. This is justified if many personal factories are eventually built based on the design. The Personal Factory prototypes, and early expansion phases are able to make items for sale. Any items sold during the development period are credited against the cost, so $66 million would be the maximum net outlay.
- 4.2 Location Cost - The unit location cost after development shall be less than $76,000 per person supported.
This covers the repeating cost for the food production, housing, and utilities capacity for each person supported per the other requirements. This is a relatively low number because automation and self-production is intended to make these things at low cost. The $76,000 is intended to cover the outside raw materials, parts, and labor which still need to be purchased. It is an average number per person when the factory is mature, and may be higher to start with. Some individual elements may be more expensive, but serve multiple people.
5. Technical Risk
- 5.1 Risk Allowances - The system design shall include allowances for performance and design uncertainties of less than 7.5% when complete.
No engineering design is perfectly understood, or built and operated exactly as intended. Therefore there will always be some uncertainty in performance, failure rate, and other parameters. A technical risk allowance is a design margin above the required performance to account for this uncertainty. In other words, we design for slightly more than we need. It is measured at the point the design is finished and building the equipment starts. Once the system is built and operating, you will find out the actual performance. The margin is intended to insure the final performance is at least at the required level. The uncertainties will be higher at the start of design, especially for something new like self-expanding factories. The intent to lower the uncertainties by methods like simulation, component tests, and prototypes. Note that technical performance risk is distinct from failures and safety hazards.
6. Safety
- 6.1 Location Risk - The system shall have a location life and property risk of less than 38% of the US 2013 average.
Safe operation is a desirable feature, so we include it as a requirement. This is to be met at the full 660 person population goal, and applies at the project-owned land and improvements. A 5/8 reduction is an ambitious goal, but we think it can be met by automation (which removes people from work hazards) and design for safety (prevent risks at the design stage).
- 6.2 Population Risk - The system shall reduce natural and human-made risks to the nearby population by 17%, including external risks created by the system.
The previous requirement was for risks of the project to it's owners and property. This one is for risks to others outside the project. We would like to have a positive impact on the nearby community. We define nearby as zones 20 km wide around the location, with 50% of the risk reduction applied in the nearest zone, 25% in the next zone, and so on. The population of the nearest zone determines the total number of people we reduce the risks for.
7. Sustainability
- 7.1 Biosphere Security - The system shall preserve 89 species outside their normal environment range, either stored or living.
In addition to present safety, we want to contribute to long term sustainability of the biosphere. The number of species is scaled to the size of the project, so we use a relatively small number here. By preserving species outside their normal range, recovery from hazards to the original population, like climate shift or human development is possible.
- 7.2 Survivability - The system shall provide 0.0085% compensation for civilization level critical risks.
Besides the biosphere, we want to contribute to the long term survival of human civilization. A project this size can only be expected to make a small contribution, therefore the requirement value is small. Examples would be helping address resource depletion or atmospheric carbon accumulation. We acknowledge this is a challenging requirement, but we think it is worth at least trying to meet it.
8. Openness
- 8.1 Open Design - Technology and design methods developed within the project shall be open for others to use. Specific instances of a design and produced items may be proprietary.
Our larger intent is not just to support one local community, but to demonstrate Personal Factories are possible and enable others to use them. We need to balance sharing the underlying technology with rewards for people who do the work. So we allow people to keep specific hardware designs and physical items private if they choose.
A.4 - Measures of Effectiveness
[edit | edit source]During the design process, attempts to meet the various requirements often affect more than one at a time. For example, higher performance and reliability often come at the expense of higher cost. To optimize a design when this happens, we use measures derived from and strongly related to the requirements, but converted to a common scoring system. How well each requirement is being met is converted by formula to a numerical score. The scores are combined, and the better design is then the one with the highest total score. For this project we will use a 100 point scale and assign a certain number of points (their weight) to each requirement according to their relative importance. The score by formula is found for each criterion, and the total score is the sum of weight x percent score for all the requirements. Note that some requirements are fixed, like the fact the project is designed to support the physical needs of a certain number of people, and thus do not get a variable score.
The measures as a whole are a mathematical model of what we think is better in a design. Like the requirements in the previous section, there is no "right answer", since they are based on human goals and choices. What the measures do is allow different people, or one person working on different parts of the project, to reach a consistent solution based on the same assumptions. In the table below we list our selected scoring items and formulas. The individual items only total to 78% because some items from a more comprehensive project are not included here. They will be included in the later design examples, and we want to be able to easily compare across projects. Therefore the total is adjusted by 100/78 to bring the score for this example to a nominal 100 point score for meeting all the targeted measures.
Criterion | Weight (points) | Scoring Formula (percent) | Notes |
---|---|---|---|
2.2 Growth (rate/yr) | 5.0 | (equivalent % annual GDP growth of all locations -2.5%) x 10 | Goal = 11%. Internal production valued as if sold at market rates |
2.3 Improved Technology (local resources) | 1.0 | % of local resources from program locations | Goal = 85%. Measure by kg (mass) or Joules (energy) |
2.3 Improved Technology (self production) | 1.0 | % of finished products from program locations | Goal = 85% by economic value |
2.3 Improved Technology (cyclic flow) | 1.0 | % of location mass flows reused | Goal = 85%. Includes local use but not production for growth or sale |
2.3 Improved Technology (automation) | 1.0 | % reduction human labor hours | Goal = 85% lower relative to current technology |
2.3 Improved Technology (autonomy) | 1.0 | % required labor and control supplied locally | Goal = 85% of necessary functions can be supplied |
2.4 Quality of Life (GDP) | 5.0 | (equivalent GDP - $20,000)/1600 | Goal = $156,000/capita. Includes value of internal production and labor |
2.6 Resources (surplus) | 5.0 | ln(material & energy output/internal use)/ln(2) x 25% | Goal = 10.5 over program life cycle. Clip at -100% |
4.1 Total development cost | 14.0 | (avg unit cost/total development cost) x 1000% | Goal = 11.7 x location cost = $890,000/capita |
4.2 New Location Cost | 14.0 | [(ln(0.25xUS capital per person/location cost))/ln(2) x 25%]+100% | Goal = $76,000/capita |
5.1 Technical Risk Allowance (%) | 5.0 | (50% - technical uncertainty allowance) x 2 | Goal = 7.5% technical allowance |
6.1 New Location Risk (relative) | 7.5 | [ln(0.25x general casualty risk/location risk)/ln(2) x 25%] +100% | Goal = 38% relative risk. Includes life and property risks |
6.2 Population Risk (relative) | 7.5 | (% reduction to general population risk) x 5 | Goal = -17% from natural and program causes. Increased risk not allowed. |
7.1 Biosphere Security (species-locations) | 5.0 | [(log(species maintained outside natural range x locations)) - 1] x 20% | Goal = 89 in vivo or stored, humans are a species |
7.2 Survivability (relative) | 5.0 | (% compensation for critical risks) x 10,000 | Goal = 0.0085%. includes all civilization level risks |
Total | 100 | Sum partial scores x weight from each line above x 100/78 |
A.5 - Functional Analysis
[edit | edit source]Analysis Approach
[edit | edit source]We want to break our Community Factory project into manageable pieces that can be individually designed. Since the factory will grow and evolve from a starter set, there is a strong time element. Thus our first division will be into phases that meet increasing levels of the total goals. Part of the growth will be how many people are in the community the project serves, so the phases also scale in amount of outputs. This keeps the equipment from being over-sized for the number of people involved. Operation on a smaller scale in the early phases should also provide some feedback for later design improvements. The Community Factory is also intended to directly support the needs of the owner-operators. Thus where the food, shelter, and utility outputs go and how they are used is an integral part of the project. We will include these items as part of our complete system analysis.
With limited people to work on the design, we cannot examine every possible alternative at present. Therefore we will make one set of functional flow diagrams as a reference point, and leave variations for future work. We plan to follow this reference design approach through the complete design cycle. Given more time and people we can then go back and look at improvements and variations.
Project Phases
[edit | edit source]
Figure 5.2-1 illustrates our division of the factory expansion starting with a conventional workshop, and six phases numbered 1A through 1F (you can click drawings for larger versions). Six is an arbitrary number of divisions of what is really a continuous expansion. We chose it as a reasonable compromise between number of phases to analyze and complexity of the additions in each step. The diagram is a partial functional flow type illustrating the time sequence, but it only shows some of the inputs and outputs. Conventional shop equipment and new parts and materials are inputs from outside the project.
The process starts with building the conventional workshop in the lowest box. We use construction tools and inputs of lumber, sheet metal, etc. and use those to assemble a building, then install the remainder of the workshop equipment. The completed conventional workshop is an output from the first function box. Along with additional outside parts and materials, we use the conventional shop tools to build the first Phase 1A expansion elements. These will be a set of added equipment that can process more materials, make new kinds of parts, etc. The loop marked "Phase 1A Expansion Elements" indicates as soon as a new piece of equipment is finished, it starts being used to help build more equipment. When the full set of Phase 1A elements are finished, we transition to the next function and start building Phase 1B. As equipment accumulates, we must also expand the building(s), roads, outdoor space for solar collectors, etc.
We continue building expansion phases in sequence through the final Phase 1F. During expansion, our ability to make our own parts and materials grows, but our target is 85% at the end of the expansion. Therefore all the phases still require new parts and materials from outside that we cannot make ourselves. The final box, "Operate Phase 1F Location" indicates the factory is complete according to this design, and outputs the full range of products for the owners, plus whatever replacement parts are needed for maintenance. This diagram does not show the outputs of final products, but all the expansion phases will do so, in increasing amounts over time.
Top Level Functions
[edit | edit source]To the outside world, the entire project can be treated as a single function box with inputs and outputs (see Figure 4.1-1). From within the design process, the edges of that function box are treated as the System Boundary, the logical division between the system we are designing and everything outside that we are not (see Figure 4.1-2). The inputs and outputs across that boundary can then be broken down into separate flows by type: Energy, Food, Water, Parts and Materials, etc. The question then becomes how to break up the sub-tasks internal to the boundary into smaller pieces. We choose as our first level of division the general type of activity: making things (Production), using things (Habitation) and moving things (Transport). This is not the only way you could divide up the project, but we think it is logical way to apply the rule of Functional Relatedness. This rule organizes functions that are more related to each other than to other functions into one group at the next higher level of a project. One reason for doing that is it places sequences of related tasks and the flows between them in a more compact and understandable layout. Another is optimizing groups of related functions is easier than trying to optimize everything at once. Changes to the related functions have less effect on the rest of the project, so they can be updated independently.
Lower Tier Functions
[edit | edit source]There is not sufficient information in the top three function boxes to identify what external flows link up with them, and what the flows are between them. To find that out, we begin a process of breaking down each function into smaller parts, identifying their inputs and outputs, and repeating until we reach individual items that are simple enough to design. Rather than creating this breakdown from scratch for each of our four example designs, we adopt the one from the reference architecture in section 3.4 as our starting point. Box and arrow type functional flow diagrams help understand how the parts of a system are connected, but they don't have room for full descriptions or technical data. We link the additional information to the diagrams by using the same names and numbers within the diagrams as reference labels on the other data.
Since the factory will grow in phases by additions to the previous phase, we don't need to create a completely new set of diagrams each time. Instead, our higher level diagrams will be based on the completed project (Phase 1F). We will make a version of the lower tier diagrams for each phase, showing what items were present in the previous phase, and what is added or changed in the current one. Therefore they represent slices in the time dimension of the project, with each slice showing the physical relationships at that time.
1. Provide Production Capacity
[edit | edit source]
Production is numbered first among our three top level functions, because logically it comes before using the products for living space or transportation. In practice, though, the other two top functions will operate mostly in parallel. Figure 4.1-3 shows the bare breakdown into second-tier functions. The core of the production flow is the sequence from extracting raw materials such as ores, processing them into finished materials such as metal alloys, fabricating parts from those finished materials, and then assembling them into finished products. To these core steps, we add a control function to issue commands to the production equipment, supply power to operate them, and store inventory as needed between steps. Lastly we have growing organics as a separate item because living things perform self-production in a fundamentally different way than human designed equipment.
Again, there are other ways the Production function could be divided up, but we think this is a logical way of grouping related tasks. The numbering sequence is also arbitrary, but more or less in time order so that flow arrows will proceed from left to right. In this form the diagram is incomplete. Next, we need to describe each function in more detail and what the flows are that connect them. This defines the scope of the tasks that a given function includes. Rather then repeat the generic descriptions from Section 3.4, please refer to those, and we will note differences and added details here.
1.1 Control Location - This function provides overall control of the Community Factory locations and systems, including production, habitation, and transport. It takes as input the designs for the locations, and for end products, which are provided from the previous R&D phase. The degree of automation in the control systems will increase by phase.
1.2 Supply Power - This function is to supply all forms of power to the Community Factory, and converting it as needed to other forms. A significant surplus is an end goal. We expect to use conventional utility power at first, adding solar furnaces for direct heating and thermal storage, and photovoltaic, wind turbine, and bioenergy systems later to increase renewable sources and reduce outside dependence.
1.3 Extract Materials - This includes local supply of raw materials, using Community Factory equipment. The end goal is to obtain the majority of total materials from new local supply, internal recycling, or from outside waste sources. Because the project needs to build the various locations, conventional heavy equipment or self-building such equipment is an early priority.
1.4 Process Materials - This includes conversion of raw materials to finished materials inventory, ready for storage, parts making, or consumption. It can use chemical, mechanical, thermal, electrical, or other processes, and operate as a continuous flow or in separate batches. Early outputs from a Community Factory may include concrete, metal shapes, glass, and wood for basic construction, with other products added later.
1.5 Fabricate Parts - This takes as input finished materials from processing or storage, plus outside materials supply. These are transformed into finished parts ready for assembly. Early processes for this function can include casting metal, glass, and concrete shapes, and machining wood and metal parts. Additional machines and processes would be added during expansion phases.
1.6 Store Inventory - This task includes storage for materials, parts, and completed items not currently in use. It includes storage for other Production functions, and long term storage for Habitation and Transport. Because of similarity, we also group environment protection and control (i.e. buildings) for the other production functions, and land for industrial tasks under this heading.
1.7 Assemble Elements - This includes combining parts and materials into higher level assemblies (collections of parts), leading to completed elements. It also includes dis-assembly of elements for maintenance or modification. Assembly includes movable elements like production machines and vehicles, and construction of fixed elements such as buildings.
1.8 Grow Organics - This includes growing microorganisms, plants, and animals to the point of harvest. Pets and ornamental plants are placed under Personal Items in Habitation. It includes the land space to grow biological products, including within Habitation areas. This land includes owned, leased, and harvest rights. Early land may be undeveloped, and used for extraction before upgrading to other purposes.
2. Provide Habitation Capacity
[edit | edit source]
The Community Factory project as a whole is intended to satisfy most of the food, shelter, and utility needs of the owners. Where the previous production top level function makes these items, the Habitation function supplies the locations where they are used. Habitation includes all types human-occupied space outside of production and transport functions. In those functions, habitation elements may be included, but they are not the primary purpose. For example, a factory building may include restrooms for the people working there, and a passenger vehicle may include heating and cooling. Conversely, a kitchen is a materials processing area, and may share equipment types like furnaces (oven) and mixers with the production area materials processing, but again. The end purpose of a kitchen is to provide food and drink to people, so it is put under the Habitation heading.
Habitation includes residential, commercial, and public use space. Buildings share common parts, like foundations and roofs, regardless of their use, and some buildings can be mixed-use. Therefore our functional breakdown is by type of human needs being met rather than by use of the building. The natural environment is often uncomfortable and sometimes hostile to humans, therefore we create shelter to modify the environment to our liking. Functionally we divide this into passive elements that protect us, and elements that actively control and modify the local environment. Once we have safe and comfortable surroundings, we next provide for the internal needs of the human body in the form of food and drink, and maintaining health. Basic items like shelter and food are necessary for everyone to live, but beyond that the majority of most people's time and occupied space is taken up by other activities which are more optional and diverse. We divide supporting these activities into the physical, which are personal items like furniture and clothing, and information, which is not tied to a specific physical item. Once we define these various functions in more detail, their required inputs and outputs then become demands which the production function needs to meet. The main habitation function descriptions are as follows:
2.1 Protect from External Environment - This includes passive protection of people and other habitation elements from weather, water, insects, and other outside factors. It also includes structural support of all habitation elements, the underlying land for it to rest on, and outdoor protective clothing.
2.2 Control Internal Environment - This function covers actively managing the internal environment created by the protective shell in terms of temperature, humidity, lighting and other factors. It includes controls and sensors, the active hardware which produces the environmental changes, lighting, windows, window coverings, and emergency systems.
2.3 Provide Food and Drink - This includes supply of food and drink materials at the point of use, local storage, food preparation, serving, dining, and disposal of food and drink wastes.
2.4 Maintain Health - This includes the actual people and their inputs and outputs. It also includes sleep, sanitation, exercise, cleaning of persons and internal environment, filtering, health monitoring, first aid, emergency services, and local examination and treatment.
2.5 Provide Personal Items - This includes the internal volume of private living and storage space, public/community space, and commercial space. It also includes the physical contents of all these spaces and decorative/non-protective clothing.
2.6 Provide Information - This includes communications, storage, and processing in all forms, for personal, commercial, teaching, entertainment, or general information. It does not include operational information for production, although they may share hardware and software elements.
3. Provide Transport Capacity
[edit | edit source]
Transport is the last by number of the three top-level functions. It is required because sources of supply, locations for production, and final points of use can all be different. Less than 100% of the owner's needs are being met internally, so we need to import some items. We also need to deliver some items for sale, move items internally at a location, and some members need to travel from home to a project site, or work offsite from the project. All the destinations may used shared transport elements, so we organize the functions by type of item transported rather than where it is going. Transport elements can be mobile or fixed (like roads), and they can be owned by the project or by other entities. Project-owned elements can be custom designs, while non-owned elements generally can't. One shared design, like a utility truck, may serve different cargo types. The functional division of tasks allows analyzing the needs for each, then considering specialized or shared equipment to satisfy them.
3.1 Transport Bulk Cargo - This includes bulk supplies, including items for sale or to build new locations. Bulk items don't need special packaging or protection.
3.2 Transport Discrete Cargo - This includes individual items that need protection from the environment, transport shocks and vibration of delivery, or need special packaging. Discrete cargo is typically smaller, thus multiple items may be delivered at once.
3.3 Transport Humans - This includes the transport of humans to and from destinations, and within a location. Humans have many of the same needs as discrete cargo, plus a desire for higher safety levels and comfort, and optional manual controls and schedule priority.
3.4 Transport Energy - This includes wired and wireless distribution of electricity, and portable sources like batteries and stored thermal energy.
3.5 Transport Fluids and Gases - These items require closed containers or fixed piping for delivery. It includes water, natural gas, and liquid fuels.
3.6 Transport Data - This includes all types of data in all forms, electronic and non-electronic. Legal rights and money are delivered via data so they are included here.
A.6 - Requirements Allocation
[edit | edit source]Allocation Approach
[edit | edit source]We set our project requirements and measures in section 5.1, and divided the project into phases and the top two levels of functions in section 5.2. The next step in the Systems Engineering process is to divide up and assign subsets of the requirements in time and space, to the phases and lower level functions. Because the factory grows over time, the complete project goals are only met at the end of the last expansion phase. So first we set reduced levels of the project requirements to meet in each phase. Next, the descriptions we wrote in section 5.2 only defined the general scope of tasks included in each function. So we allocate the end point performance levels, operations, and maintenance subsets for each function in more exact terms. The intent is that the sum of the assigned detailed requirements satisfies all the project level goals. Finally, we can define the reduced levels for each function in each phase.
Phase Requirements
[edit | edit source]If we examine the requirements in section 5.1, some will change relatively less, or not at all, as the factory evolves through its growth phases. Therefore we will consider them individually. Since we do not have an optimized design yet, we do not know the best way to divide up the requirements by growth phase. Instead, we will make what we think are reasonable assumptions as a starting point. We expect this first draft of the phase requirements will be updated as the design progresses. The discussion that follows uses the same numbering as in section 5.1.
As a first generation design for a self-expanding factory we do not expect to reach 100% performance levels in any part of it. Instead, we assume a general goal of 85% for features with variable performance levels. Across phases, we further assume that the easiest tasks are tackled first, and so the performance levels increase rapidly at first, with decreasing increments in each phase. Numerically, we divide meeting the goals into 6 phases as a geometric progression by raising the 15% unmet goal at the end to the 1/6 power. Thus each phase has a 72.9% smaller unmet goal, and the met goals, rounded to the nearest percent, become 27%, 47%, 61%, 72%, 80%, and 85%. The steps are 27, 20, 14, 11, 8, and 5% per phase, reflecting the assumed increasing difficulty of reaching 100%.
1. Objectives
- 1.1 Project Goal - The overall goals of the factory are to be locally owned and support the physical needs of the owners. We set both of these to be met 85% at the end of the sixth phase (1F). Any project needs some funding and development to get started, and we allow a large amount of that to be outside the local area at first. This allows us to tap a wider range of financial and technical capacity as a distributed open-source project. Over time, the particular project location grows, and we expect increasing participation by local members who end up owning and operating it themselves. Concurrently, the factory will meet a growing percentage of their physical needs. By phase we scale the local ownership and support levels according to the percentages in the previous paragraph. We do not try to design the factory to provide services that need a human element, like medical care, but we can provide the physical needs that make those services possible, like buildings and utilities. We assume that project members and residents will meet the services part of their needs by providing them to each other, or get them from outside sources.
- 1.2 Project Scale - The end goal is to add support for 75 people per year up to 660 people total. One of the growth methods for a Seed Factory is by scaling - building larger versions of equipment than was in the starter set. Starting with smaller equipment requires less starter funds, and allows early use of the ability to self-expand. The set of developers and owners is also expected to start small. Even at the end of the growth phases, some percentage of outside supplies will be needed, and this will increase along with production scale. Also, in the later growth phases we are making more of the harder to make items, which would require relatively more equipment to produce. So we will assume the output rate will grow more slowly in percentage terms by phase. By phase the number of added people/year supported will assume starting values of 0.25, 1, 4, 12, 32, and 75. The increases are 400%, 400%, 300%, 267%, and 234% between phases.
- 1.3 Choice - Another important goal is choice for the owner/operators, including what products the factory will make. However, we cannot design the factory without knowing something about the outputs it will produce. We will use the US Consumer Price Index as a proxy for what people want, since it represents averages from surveys of what people actually spend their money on. By phase we will assume the most basic goods, like food and shelter, are satisfied first. For calculation purposes, we will use typical mixes of items within the goods categories. We will keep in mind factory flexibility, so that the actual owners can choose the production mix within some reasonable range.
2. Performance
- 2.1 Location - The end goal is a design which will operate in the middle 90% of environments where people live. The first copy will be built in a particular location, which we are assuming to be near Atlanta, GA. Thus by phase we will start out designing for that location, and widen the design range to accommodate the full 90% range by the end of the growth cycle. In some cases, the design differences would be small between the versions, and only one design would be done, to avoid changing it.
- 2.2 Growth - The growth rate in this requirement is explicitly for after the growth phases, so we skip it as a phase requirement.
- 2.3 Improved Technology - The first five of these requirements (Local Resources, Self Production, Cyclic Flows, Automation, and Autonomy) all have final goals of 85%. We therefore use the general phase targets noted in the paragraph prior to "1. Objectives" above. The requirement to limit complexity for the starter set begins at 7 major elements. We still don't want to use every existing manufacturing process at the end of the growth phases, since that would require a lot of design work and equipment. Using our scoring formula for complexity in reverse, we can set targets of 7, 13, 21, 39, 48, and 55 major elements by phase. Setting targets like this forces us to choose flexible equipment and think about adapting one device for multiple tasks.
- 2.4 Quality of Life - Meeting physical needs can cover a wide range of quality. For example, a log cabin and a mansion both provide shelter, but at vastly different levels. The measure here is the monetary equivalent of goods provided from factory production plus other income of residents. Even at the end of growth, residents will do some outside work, and in earlier phases will do relatively more, so we include that portion at the Jan 2013 US average GDP/person of $50,750/year. This applies to the 23% of all needs which are services, and the part of the goods sector not met by factory production. As the factory grows, we expect the quality and quantity of products to increase, so we estimate their value will go as the square of needs being met. This gives values of 10%, 30%, 51%, 72%, 88%, and 100% relative to the final value.
- At the end of phase 1F, the factory is providing 85% of the 77.1% goods sector = 65.5% of total needs. The other 34.5% is assumed to generate $17,500 value, giving $138,500/year as the required value of the factory production. Scaling by the percentages in the previous paragraph, we get requirements of 14, 41.5, 70.5, 100, 122, and 138.5 k$/person/year output value by phase.
- 2.5 Data - Sharing of project experience and data is not variable with the growth phases, so we skip this as a phase requirement.
- 2.6 Resources - The intent of this requirement is a highly productive system with a surplus of energy and materials production once growth and construction is completed. For earlier phases we will look at the ratio of production vs. factory maintenance and support for what has been built to that point. We scale it according to the scoring formula for this requirement, giving ratios of 2.1, 3.7, 5.4, 7.3, 9.2, and 10.5 by phase.
3. Time
- 3.1 Completion Time - This does not apply as a separate requirement at the project level, it is covered by output rate under project scale. How fast the growth phases are completed will depend largely on how many people participate, and thus how fast the design is completed and how much in funds and labor is available for construction. We cannot predict those, but we can set a requirement assuming they are available. Based on large scale construction project experience, we will assume each phase requires a minimum of 14 months to finish after the previous phase, with Phase 1A taking 24 months to design and build, and 1F taking 84 months total, each phase taking 12 months longer. Thus in the best case there is a large amount of overlap in starting design of each phase. If less people and funds are available, the start of later phases will be delayed.
- 3.2 Operating Life - At the project level the service life is intended to be indefinite, given maintenance, repair, and replacement. Given that this project is a factory, and we build it from starter kit to full expansion the first time, by merely repeating the building process we can achieve a long term service life. However, building new items from scratch may not be the most efficient way to do this, and the service life of individual parts is not specified. We cannot specify the best way to meet this requirement by phase until the design is more complete. Instead we will include at each phase a requirement to optimize the design for maintenance, repair, and replacement for sustained permanent operation.
4. Cost
At the start of design we are setting cost goals. As the work progresses, we will later develop cost estimates, and then actual costs. The goals are intended to keep costs within reasonable levels in relation to meeting the other requirements. In particular, the ratio of cost to performance is often considered the most important measure of a project.
- 4.1 Total Development Cost - This includes the one-time non-recurring costs for technology development and system design. The early phases use smaller versions of the factory equipment because they are designed for fewer people. Their complexity, and thus the design work, is about the same, so the relative design cost is higher at the start. Additionally, some items, like the factory control software, only need to be designed once in the early phases, and then slightly modified for a larger factory with more machine types in later phases. Finally, smaller equipment and fewer different machines are less expensive to prototype. Combining all these factors, we use our scoring formula to set goals of 37, 21.3, 16.4, 13.9, 12.5, and 11.75 times the location cost per phase, to get 13.875, 4.58, 2.46, 1.53, 1.09, and 0.893 M$/person capacity. This is multiplied by phase production capacities of 0.25, 1, 4, 12, 32, and 75/year to get development cost goals of 3.5, 4.6, 9.8, 18.3, 35, and 67 M$/phase. As an open-source project, much of this cost may be contributed design and construction labor.
- 4.2 Location Cost - The value of $76,000/person repeating cost is at the end of Phase 1F, and covers outside parts, materials, and labor besides what the project produces internally. At earlier phases this value will be larger, because the factory is less capable of producing items, and therefore more must be purchased. For the earlier phases, we apply the relative score scoring formula to set values of 375, 215, 150, 110, and 87 k$/person.
5. Technical Risk
- 5.1 Risk Allowances - The goal is to reach 7.5% performance and design uncertainties at the point building the last growth phase starts. The earlier phases will have less experience and fewer completed designs, so we will scale the risk allowance by our scoring formula to be 36.5%, 26.5%, 19.5%, 14%, 10%, and 7.5% by phase.
6. Safety
- 6.1 Location Risk - We have set ambitious safety goals for the project, which can only be met if people change how they live and work. The early phases will make fewer such changes and introduce construction and new production processes with risks that are poorly understood at first. Later phases will have more experience with these same processes and better understanding of how to optimize their safety. We accept higher early risks because of the smaller number of people involved and future benefits. Therefore the goals will be scaled using our scoring formula to 190%, 108%, 74%, 54%, 44% and 38% of US averages by phase.
- 6.2 Population Risk - The goal is to reduce natural and human-made risks to the nearby population by 17%. Rather than scale this by phase, we will scale it by the resident population supported relative to the final target of 660. A wide variety of risks can be addressed, such as providing fire-fighting assistance or severe weather shelters.
7. Sustainability
- 7.1 Biosphere Security - The goal is to preserve 89 species outside their normal environmental range. We will also scale this requirement by resident population, thus 1 species per 7.4 population.
- 7.2 Survivability - The goal is to provide 85 millionths compensation for civilization level critical risks. We scale this requirement by resident population, thus 1 millionth per 7.75 population. An example would be to reduce atmospheric carbon accumulation by the given amount relative to the whole world.
8. Openness
- 8.1 Open Design - The intent is for the project to share the technology and design methods it develops. This requirement does not change by expansion phase.
Assign Functional Requirements
[edit | edit source]Having made our assumed distribution of requirements across the growth phases, we now turn to the functional elements we have divided the project into. The identity of the functions is preserved across the growth phases. Thus the function names, numbers, and flows linking them to other functions do not change from one phase to the next. The quantities, however will change by phase. This includes the possibility that a given function is not used at all in an early phase, and the quantities are zero.
We identified three top level functions and 18 second-tier functions, so we break up and assign subsets of the requirements to each of them. We take care that the subsets add up numerically to the next higher level, and that each requirement is accounted for somewhere in the project. The descriptions that follow are for assignments to the top level functions.
Top Level Functions
[edit | edit source]
Our three top level functions are Provide Production Capacity, Provide Habitation Capacity, and Provide Transport Capacity. We will refer to them as Production, Habitation, and Transport for short.
1. Objectives
- 1.1 Project Goal - The levels of local ownership are distributed to all three functions such that the total meets the goals of the phase. They may vary by functional element. Supporting the physical needs of the owners is assigned to the point of use, which is Habitation and Transport. The required levels of Production outputs are then derived from the flows necessary to meet those needs.
- 1.2 Project Scale - The number of new people supported per year is assigned to all three functions by creating Production, Habitation, and Transport Scale requirements, and assigning the proper number of people/year by phase.
- 1.3 Choice - The choice of project locations, internal organization, and operations by members and residents is assigned to the future planning task of the Control Location function of Production. That task will include mechanisms to take inputs from people, and incorporate them into the project plans.
2. Performance
- 2.1 Location - The operating environment is constant across the top three functions, since the project is defined as locally operated. It is passed down unchanged to each of them.
- 2.2 Growth - The capacity for growth of 11%/year is explicitly levied against all three top functions in the system level requirements, so we pass it down to each. It only applies once Phase 1F is built and capacity for 75 people per year is reached. The inherent growth rates in earlier phases will be derived from the level of surplus resource production. Actual growth rates, as opposed to inherent growth, will depend on the number of people and sources of funds for the project. By analogy to a forest, the inherent growth rate of the trees is fixed, but you can plant more trees and expand the forest faster than that.
- 2.3 Improved Technology - The general requirement to increase levels of self-production, recycling, and other technical features is mostly assigned to Production, but the design of Habitation and Transport elements have to accommodate those levels. So we impose a derived requirement on them to use what Production makes and return items to be recycled. This general requirement is divided into more specific ones.
- 2.3.1 Local Resources - Providing a percentage of continuing matter and energy needs from local resources is mainly assigned to Production. Some resources may be met by Habitation, such as rainwater collection or rooftop solar panels. Percentage is measured in economic terms. Continuing needs are after initial construction. Higher levels of outside supplies may be needed at first.
- 2.3.2 Self Production - The requirement is to provide a growing percentage of economic value for the owners internally from the project. Use of homes and personal transportation are part of this economic value. We further divide the overall percentage goal into 75% from Production, 15% from Habitation, and 10% from Transport. That division is somewhat arbitrary and may need to evolve by growth phase, so long as the total adds to 100%.
- 2.3.3 Cyclic Flows - The requirement is to recycle and reprocess a growing percentage of local waste flows. The first part of this, physical delivery of wastes back to production, is allocated to all three main functions. Conversion of wastes back to useful form is assigned to Production. Outside scrap and wastes may be used as a source of materials, but this is not counted as part of the recycled percentage, it is new input.
- 2.3.4 Automation - The requirement is to reduce human labor by a significant percentage relative to the US average. Some reduction through automation is feasible for items like household maintenance, food preparation, and vehicle driving. Most of the gains, though, would be for Production. We tentatively apply 10% each to Habitation and Transport (especially internal transport within a location), and 80% to Production automation.
- 2.3.5 Autonomy - Local control of production planning, operations tasks, and maintenance will grow in parallel with percentage local ownership (Requirement 1.1). This is imposed on all three top-level functions to be executed by local humans and control equipment. The percentage for each function will vary, but the combined average will meet the phase percent goal. Habitation will have a higher level of local control by the residents, but Production has a larger quantity of tasks to control. This is due to the complex operations within Production, and that overall location responsibility is also assigned to the Production "Control Location" function.
- 2.3.6 Complexity - This requirement is specifically about the number of Production elements, therefore it is applied to that function, and the part of Transport that involves production tasks.
- 2.4 Quality of Life - The intent is to provide an increasing quality of life for project members by phase, in terms of equivalent GDP. This includes the value of directly used factory products such as food and home-building materials, sale of surplus production to generate income, and outside/non project work. Since requirement 2.6 calls for a high level of surplus production, we will allocate 75% of this requirement to Production. Habitation and Transport are assigned 20 and 5% respectively, based on their relative proportions in the Consumer Price Index. Their annual GDP contribution is converted capital values using typical lease rates of 8% for Habitation, and Transport vehicle value declining at 12%/year plus operating and maintenance expenses. This results in a Phase 1F goal of $400,000/person of Habitation value. Transport is more complicated to calculate, and we will defer that to later.
- 2.5 Data - Sharing of project experience and data is imposed mainly on the Production function, since it already contains design and operations data. Some data may be collected from Transport and Habitation, with the limitation that personal data will be protected.
- 2.6 Resources - This requirement for a large surplus in materials and energy over internal needs is allocated to the Production function, and is measured by continuing needs of that function only, not total needs counting Habitation and Transport.
3. Time
- 3.1 Completion Time - This requirement is mostly allocated to building the Production elements, and somewhat to Transport which supports production. The minimum phase design and construction schedules are passed directly to these functions. The schedule for Habitation and personal Transport elements depends on how many people are involved in the project that need them. Therefore actual, as opposed to minimum, schedules, cannot be defined in advance. The planning function within Production will accept inputs from people on an ongoing basis, and adjust progress from phase to phase and construction rates within phases as needed.
- 3.2 Operating Life - As noted in the phase requirements for operating life, the project as a whole has an indefinite service life with ongoing maintenance, repair, and replacement. We pass down a requirement to optimize each of the three top level functions for an indefinite life assuming maintenance. That optimization will include the fact the project has its own production capacity, assembly areas, and construction equipment, and can therefore do much of its own maintenance tasks.
4. Cost
- 4.1 Total Development Cost - Total development cost is allocated as a simple sum of the various functions that make up the project. We will use 60% for Production, 20% for Habitation, and 20% for Transport, times the phase development as a first approximation. As the design progresses, we will very likely update these values. Development cost is net of any sales or income from the project, thus it represents the maximum outlay at any point in the phase.
- 4.2 Location Cost - Location cost is also allocated as a sum of the project function costs. As an initial estimate, we will use 40% for Production, 40% for Habitation, and 20% for Transport, times the phase location cost per person. The relatively higher Habitation estimate versus Development Cost for Production is because Habitation will tend to use repetitive construction elements, while Production will be adding new and different elements in each phase. Again, these first estimates will very likely be updated as the design evolves.
5. Technical Risk
- 5.1 Risk Allowances - This requirement is the amount of over-design to account for uncertainties in performance. It is an estimate before the final hardware is built and tested, at which point you know the actual performance. The allowance is to ensure the final design performs at least as well as the requirements specify. It is particularly important for a complex and interconnected system such as this one, because a deficiency in one element can cause others to under-perform, and in turn these others can affect still more parts of the system. Therefore we build in a positive bias above the required levels.
- We allocate this risk according to an estimate of how much new design is in each of the three top level functions. Much of Habitation will be conventional building materials, so it gets the lowest share, 15%. Transport may use more new designs, such as robotic vehicles, so we give it a 25% share. The remaining 60% is allocated to Production because design for self-production, integrating many different processes, and automated control of all of it have a large degree of new design. These allocations are combined to reach the phase allowances for the project as a whole.
6. Safety
- 6.1 Location Risk - This consists of life and property risk internal to the project. Until a risk analysis is done, we don't have a good way to estimate where these risks are, and how they could be reduced. Therefore the risk levels relative to US averages is divided among the top level functions such that the total goal is met, but specific percentages are not specified at this time.
- 6.2 Population Risk - The goal is to have a positive impact by reducing net risk from the project to the nearby population. This consists of two parts. The first is new risks caused by the project. Particular attention needs to be given to Production processes and off-site transportation. The second is active risk reduction by positive changes supplied by the project. Possible mechanisms include a higher tax base funding community improvements, donated goods and services, supplying safer products, or other means. Prior to doing a risk analysis, we assign 50% of this requirement to Production, and 25% each to Transport and Habitation, scaled to the resident population goal of 660 people. We expect these values to be updated.
7. Sustainability
- 7.1 Biosphere Security - Natural species will exist at and near the project location, and we take it as a default assumption not to endanger these local species. Preserving other species outside their normal range is an active effort above this. The intent is for the project to contribute to long term sustainability of the biosphere. The level of effort is scaled by the size of the resident population. Prior to analyzing the most effective way to do this task, we will assign it 50% each to Production and Habitation, because both Growing Organics and landscaping and pets in Habitation involve living things. Species preservation may be done locally at the project, or at other locations or through agencies if that is more efficient.
- 7.2 Survivability - This requirement is also scaled to resident population. We assign it to Production because the most likely areas to reduce civilization level risks are in energy production and recycling. Because we will have design and production capacity, there is also the possibility of contributing to larger projects.
8. Openness
- 8.1 Open Design - The general requirement is to share project technology and design methods so that others can benefit from it, and hope that others outside the project will share their developments in return. Project members need incentive to contribute their own work, thus specific instances of designs may be kept proprietary if desired, and the physical hardware and products are owned by them. Besides proprietary designs, the other limitation on general openness is protecting the personal privacy of members and residents. We assign this requirement to the Production function, because project data will be collected and stored in that function's data networks, and external communication and privacy protection is best implemented there.
Lower Tier Functions
[edit | edit source]
Having allocated the requirements to the three top level functions, we would continue this process in later rounds of the design work. Requirements would be allocated to the second and lower tiers, until we reach functional elements that can be individually designed. Section 5.0 as a whole is intended to be an example of how to apply the design process to a particular project. We think that describing the assignment of requirements to every lower level function, and their quantities by phase, is too much detail to include here in the main text of the book. It would break the flow of showing how to do the design work. Instead we will place most of those details in Section 9.0 - Design Notes, and refer readers there if they are interested.
To complete this first round of requirements allocation, and as a starting point for the next lower tier, we can gather the assigned requirements by function into tables. These then serve as the input requirements for the parts of the system in the same way the system requirements in Section 5.1 serve for the project as a whole. For completeness, the tables list requirements not applied to that function, but in subsequent work they are skipped and only the applied subset is analyzed. The values given include the variation by phase.
Requirement Title | Text |
---|---|
1.1 Production Goal | Contribute to local ownership and meeting the owner's physical needs at 27, 47, 61, 72, 80, and 85% levels by phase. |
1.2 Production Scale | Produce location elements for 0.25, 1, 4, 12, 32, and 75 people/year by phase, to reach a capacity of 660 people. |
1.3 Choice | Accept owner inputs for locations, organization, and production operations and incorporate these into project planning. |
2.1 Location | Design for operation initially near Atlanta, GA, to reach any temperate environment (middle 90% of population) in phases. |
2.2 Growth | Include capacity to increase production by 11% per year compounded, after expansion phases, as measured by economic value of the output. |
2.3.1 Local Resources | Provide 27, 47, 61, 72, 80, and 85% by phase of continuing matter and energy needs from local resources, as measured by economic value. |
2.3.2 Self Production | Produce 75% x (27, 47, 61, 72, 80, and 85% by phase) of location economic value from Production, with the remainder from outside work. |
2.3.3 Cyclic Flows | Recycle and reprocess 27, 47, 61, 72, 80, and 85% by phase of location waste flows, measured by mass. |
2.3.4 Automation | Contribute 80% of human labor reduction goal of 27, 47, 61, 72, 80, and 85% by phase, relative to US average. |
2.3.5 Autonomy | Control Production share and overall location operations and maintenance to reach 27, 47, 61, 72, 80, and 85% by phase for total location. |
2.3.6 Complexity | Limit the number of major Production elements to 7, 13, 21, 39, 48, and 55 by phase, not counting attachments, bits, tooling, or conventional small shop tools. |
2.4 Quality of Life | Contribute 75% of 14, 41.5, 70.5, 100, 122, and 138.5 k$/person/year by phase in equivalent value from Production, referenced at January 2013 prices. |
2.5 Data | Share Production and general location experience and data with owners and residents, the surrounding community, and beyond, while protecting personal privacy. |
2.6 Resources | Produce 2.1, 3.7, 5.4, 7.3, 9.2, and 10.5 times internal needs, by phase, for maintenance and support of the Production elements, in products and energy. |
3.1 Completion Time | Given people and funding, complete Production elements within 24, 36, 48, 60, 72, and 84 months by phase, with 2 months minimum between starts. |
3.2 Operating Life | Design Production elements for an indefinite service life with optimized maintenance, repair, and replacement. |
4.1 Development Cost | Limit development cost for Production to 60% of 3.5, 4.6, 9.8, 18.3, 35, and 67 M$ by phase, net of sales and including in-kind contributions. |
4.2 Location Cost | Limit outside incremental Production cost/person to 40% of 375, 215, 150, 110, 87, and 75 k$ by phase, not including self-production. |
5.1 Risk Allowances | Limit Production performance and design uncertainties to 60% of location design margins of 36.5, 26.5, 19.5, 14, 10, and 7.5% by phase. |
6.1 Location Risk | Limit Production contribution to location total life and casualty risk of 190, 108, 74, 54, 44, and 38% of US averages by phase. |
6.2 Population Risk | Reduce life and casualty risk to nearby population from Production by 50% of 17% times 1/660 of resident population. |
7.1 Biosphere Security | Support preserving 50% of 89 species outside their normal environment range times 1/660 of resident population. |
7.2 Survivability | Provide 0.0085% compensation for civilization level critical risks, times 1/660 of resident population. |
8.1 Open Design | License project technology and design methods on open terms, while specific designs and physical items may be privately owned. |
Requirement Title | Text |
---|---|
1.1 Habitation Goal | Contribute to local ownership and meeting the owner's physical needs at 27, 47, 61, 72, 80, and 85% levels by phase. |
1.2 Habitation Scale | Operate and maintain Habitation elements for 0.25, 1, 4, 12, 32, and 75 new people/year by phase up to 660 total. |
1.3 Choice | Provide for owner and resident design and modification choice for Habitation, within overall location and project limits. |
2.1 Location | Design for operation initially near Atlanta, GA, to reach any temperate environment (middle 90% of population) in phases. |
2.2 Growth | Include capacity to increase Habitation occupancy by 11% per year compounded, after total of 660 is reached. |
2.3.1 Local Resources | Design Habitation elements to use 27, 47, 61, 72, 80, and 85% local resources by phase for operations and maintenance. |
2.3.2 Self Production | Produce 15% x (27, 47, 61, 72, 80, and 85% by phase) of location economic value from Habitation. |
2.3.3 Cyclic Flows | Return 27, 47, 61, 72, 80, and 85% of Habitation waste mass by phase to Production for recycling. |
2.3.4 Automation | Contribute 10% of human labor reduction goal of 27, 47, 61, 72, 80, and 85% by phase, relative to US average. |
2.3.5 Autonomy | Control at least 27, 47, 61, 72, 80, and 85% by phase of Habitation operations and maintenance locally. |
2.3.6 Complexity | Production complexity does not apply to Habitation. |
2.4 Quality of Life | Provide Habitation elements capital value by phase of 80, 150, 220, 300, 350 and 400 k$/person, referenced at January 2013 prices. |
2.5 Data | Collect Habitation experience and data while protecting personal privacy. |
2.6 Resources | Surplus materials and energy production does not apply to Habitation. |
3.1 Completion Time | Reach element installation rates within 24, 36, 48, 60, 72, and 84 months by phase, on 2 month start intervals, given people and funding. |
3.2 Operating Life | Design Habitation elements for an indefinite service life with optimized maintenance, repair, and replacement. |
4.1 Development Cost | Limit development cost for Habitation to 20% of 3.5, 4.6, 9.8, 18.3, 35, and 67 M$ by phase, net of sales and including in-kind contributions. |
4.2 Location Cost | Limit outside incremental Habitation cost/person to 40% of 375, 215, 150, 110, 87, and 75 k$ by phase, not including self-production. |
5.1 Risk Allowances | Limit Habitation performance and design uncertainties to 15% of location design margins of 36.5, 26.5, 19.5, 14, 10, and 7.5% by phase. |
6.1 Location Risk | Limit Habitation contribution to location total life and casualty risk of 190, 108, 74, 54, 44, and 38% of US averages by phase. |
6.2 Population Risk | Reduce life and casualty risk to nearby population from Habitation by 25% of 17% times 1/660 of resident population. |
7.1 Biosphere Security | Support preserving 50% of 89 species outside their normal environment range times 1/660 of resident population. |
7.2 Survivability | Civilization level risk reduction does not apply to Habitation. |
8.1 Open Design | Licensing project technology and design methods does not apply to Habitation. |
Requirement Title | Text |
---|---|
1.1 Transport Goal | Contribute to local ownership and meeting the owner's physical needs at 27, 47, 61, 72, 80, and 85% levels by phase. |
1.2 Transport Scale | Operate and maintain Transport elements for 0.25, 1, 4, 12, 32, and 75 new people/year by phase up to 660 total. |
1.3 Choice | Provide for owner and resident design and modification choice for Tranport, within overall location and project limits. |
2.1 Location | Design for operation initially near Atlanta, GA, to reach any temperate environment (middle 90% of population) in phases. |
2.2 Growth | Include capacity to increase Transport quantity by 11% per year compounded, after expansion phases. |
2.3.1 Local Resources | Design Transport elements to use 27, 47, 61, 72, 80, and 85% local resources by phase for operations and maintenance, including fuel. |
2.3.2 Self Production | Produce 10% x (27, 47, 61, 72, 80, and 85% by phase) of location economic value from Transport. |
2.3.3 Cyclic Flows | Return 27, 47, 61, 72, 80, and 85% of Transport waste mass by phase to Production for recycling, not including fuel. |
2.3.4 Automation | Contribute 10% of human labor reduction goal of 27, 47, 61, 72, 80, and 85% by phase, relative to US average. |
2.3.5 Autonomy | Control at least 27, 47, 61, 72, 80, and 85% by phase of Transport operations and maintenance locally. |
2.3.6 Complexity | Limit the number of major Transport elements used for Production, and count them in the Production limits by phase. |
2.3 Technology - Autonomy | Control at least 85% of transport functions locally. |
2.4 Quality of Life | Contribute 5% of 14, 41.5, 70.5, 100, 122, and 138.5 k$/person/year by phase in equivalent value from Transport, referenced at January 2013 prices. |
2.5 Data | Collect Transport experience and data while protecting personal privacy. |
2.6 Resources | Surplus materials and energy production does not apply to Transport. |
3.1 Completion Time | Reach element production rates within 24, 36, 48, 60, 72, and 84 months by phase, on 2 month start intervals, given people and funding. |
3.2 Operating Life | Design Transport elements for an indefinite service life with optimized maintenance, repair, and replacement. |
4.1 Development Cost | Limit development cost for Transport to 20% of 3.5, 4.6, 9.8, 18.3, 35, and 67 M$ by phase, net of sales and including in-kind contributions. |
4.2 Location Cost | Limit outside incremental Transport cost/person to 40% of 375, 215, 150, 110, 87, and 75 k$ by phase, not including self-production. |
5.1 Risk Allowances | Limit Transport performance and design uncertainties to 25% of location design margins of 36.5, 26.5, 19.5, 14, 10, and 7.5% by phase. |
6.1 Location Risk | Limit Transport contribution to location total life and casualty risk of 190, 108, 74, 54, 44, and 38% of US averages by phase. |
6.2 Population Risk | Reduce life and casualty risk to nearby population from Transport by 25% of 17% times 1/660 of resident population. |
7.1 Biosphere Security | Preserving species outside their normal environment only applies in Transport support to the Production and Habitation functions. |
7.2 Survivability | Civilization level risk reduction does not apply to Transport. |
8.1 Open Design | Licensing project technology and design methods does not apply to Transport. |