Engineering Acoustics/Sonic Supercharging of 2 Stroke Engines
Sonic Supercharging of 2 Stroke Engines
[edit | edit source]This page of the Engineering Acoustics Wikibook discusses the merits and design of Tuned Pipes for 2 Stroke Engines. For introductory material on 2 Stroke Engines please see the following links:
HowStuffWorks 2 Stroke Engines
Introduction
[edit | edit source]For a 2 stroke engine the tuned pipe is the section of the exhaust system that begins at the exhaust port and ends at the end of the converging section. A tuned pipe is made of between 3 and 4 characteristic sections depending on the desired effect. The figure below depicts cross sections for 3 typical configurations of tuned pipes as well as a straight pipe:
The purpose of straight and tuned pipes is to utilize the pressure waves originating from the exhaust port to assist the breathing of the engine. This is achieved by designing the pipe in such a way that positive and negative reflected waves arrive back at the exhaust port at an instant when a low or high pressure is desired. This is beneficial for two stroke engines because unlike four stroke engines, they do not have dedicated intake and exhaust strokes and valves.
The following picture labels the various elements of a two-stroke engine which are referred to in this Wikibook page.
Furthermore; abbreviations will help as well:
- In order of accensding crank angle
- TDC - Top Dead Center, 0 deg
- EPO - Exhaust Port Open
- TPO - Transfer Port Open
- BDC - Bottom Dead Ceneter, 180 deg
- TPC - Transfer Port Close
- EPC - Exhaust Port Close
For introductory material on 2 Stroke Engines please see the following links:
HowStuffWorks 2 Stroke Engines
Straight Pipe
[edit | edit source]The goal of a tuned straight pipe in this application is to use the reflected negative pressure waves from the open end of the pipe to help draw out the exhaust gases. By selecting the appropriate length of the pipe, the reflected rarefaction wave arrives at the exhaust port just as the transfer port opens thus assisting the flow of fresh mixture into the cylinder, and exhaust gases out of the cylinder. The figure below illustrates this action. In the figure, even though the piston has reached bottom dead center (BDC), fresh mixture continues to enter the cylinder because the rarefaction wave causes P2 to be smaller than P1. A key point to note is that the velocity with which the pressure and rarefaction waves travel down and up the exhaust pipe is for the most part independent of the engine operating frequency (RPM). Due to this fact, the conclusion must be made that for a given pipe length there is an optimal RPM for which the waves will arrive producing the greatest benefit for the breathing of the engine. At this optimal RPM, the engine breathes significantly better and hence produces a noticeable increase in output power. This effect is quantified by calculating the ratio of fresh mixture to exhaust gases within the cylinder as the compression stage begins at EPC. If the rarefaction wave is very large, it is possible that fresh mixture is pulled into the exhaust pipe while both transfer and exhaust ports are open. This phenomenon is known as short circuiting the engine and produces undesired effects such as a decrease in fuel economy and an increase in release of volatile organic compounds. These negative effects can be mitigated by designing the exhaust system such that either no fresh mixture is pulled into the exhaust pipe (i.e. perfectly tuned straight pipe) or further utilizing the exhaust pressure wave to inhibit short circuiting. For performance two-stroke engines, the second solution is most often employed by means of a tuned exhaust pipe known as a tune pipe.
Tune Pipe
[edit | edit source]With a converging-belly section-diverging type tune pipe the goal is to have the diverging section create a returning rarefaction wave and the converging section create a returning pressure wave. The belly section acts as an appropriate time delay between the returning waves such that the pressure wave arrives at the exhaust port after the transfer port has closed. This pressure wave pushes the excess fresh mixture in the exhaust pipe from a short circuit, back into the cylinder. Here the short circuited fresh mixture is actually desired since this allows the returning pressure wave to "super charge" the cylinder giving it more fresh mixture than if the cylinder were filled at ambient pressure. This is a similar result to turbo-charging or super-charging a four-stroke engine. If the mixture contained within the cylinder before combustion occurs were allowed to expand to ambient pressure, its volume would be larger than the displacement of the engine. This phenomenon is quantified as volumetric efficiency; it is calculated as the ratio of the ambient pressure volume of the fresh charge, divided by the displacement volume of the engine. The operation of a two-stroke engine equipped with a properly tuned pipe is shown in the animation below, for a step by step description of the process, please follow the link below the animation.
There are exhaust manufacturers now that are mating up tuned pipes to tuned (ported) engines to get the best possible 'supercharging effect' at given rpm's. In the past a tuned pipe would have been tested on a stock engine but the length and shape of the pipe will differ on a 'tuned' engine because of the way it is able to rev higher .
Tune Pipe Design Geometry
[edit | edit source]The most basic form of a tune pipe is shown in the figure below with corresponding wave equations.
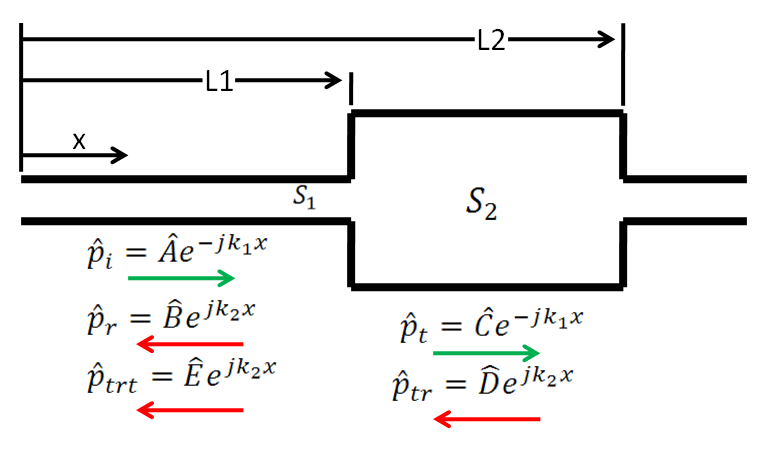
This pipe consists of an expansion chamber which serves to create both the returning rarefaction and pressure waves. From reference [1], we know that wave speed in the pipe is effectively independent of engine RPM and largely dependent on temperature of the gases in the pipe. This means that a tune pipe with basic geometry operates optimally for only one specific RPM, as the engine RPM deviates from this optimal value the timing of the arrival of the returning waves is less optimal for the volumetric efficiency. The relation between the volumetric efficiency and the engine RPM is characterized qualitatively by the following graph:
Although the basic tune pipe performs the desired task of increasing the volumetric efficiency, the narrow RPM band width for which increased power is available reduces the practicality of the basic pipe since engines are typically required to operate within a wide range of RPM. One way to broaden the effective RPM band width of a pipe is to taper the pipe at sections of increasing and decreasing cross section. To understand how this works, we can represent a tapered section as many small step increases/decreases in cross section. Each step will produce transmitted and reflected waves in the same way as the basic geometry; however, the overall effect is weaker waves with longer wave lengths arriving back at the exhaust port. Although the waves have smaller peak amplitudes, the effect on volumetric efficiency is greater due to the longer interaction times of the waves with the cylinder and crankcase. If the number of steps increased to n diverging steps and m converging steps, the equations shown represent the plane waves as well as the transmission and reflection factors for each change in cross section.
The graph below shows qualitatively how pressure at the exhaust port varies with crank angle for both basic and tapered pipe geometry.
The important differences to notice in the graph are the relative magnitudes and durations of the positive and negative pressure waves arriving back at the exhaust port at TPO and EPC. In this graph, if we pin down the waves with respect to time along the horizontal axis and then we increase or decrease the RPM, the effect will be that the positions of the port timing will no longer match up with the same positions of the waves. This is due to the fact that, as mentioned above, the wave speed is independent of RPM. In more detail if we increase the RPM it would have the effect of shrinking the port timing scale while keeping EPO in the same position. If we increase the RPM, the port timing scale expands with EPO remaining in the same position.
Looking at things the other way around, if we change some aspects of the pipe geometry we can see how they change wave propagation in the pipe and hence operation of the pipe with respect to the engine.
- Length of the pipe between the exhaust port and the diverging section (L1) - this length set by the difference in crank angle between EPO and TPO and the desired effective RPM range of the pipe. Making the section longer would fit a lower RPM range or a greater difference between the crank angle of EPO and TPO.
- Length of the belly section - this length is set by the difference in crank angle between TPO and EPC and the desired effective RPM range of the engine. This length and L1 are interdependent since the crank angles are also interdependent, (e.g. EPC=(0-EPO)).
- The angle of the diverging/converging sections - changing this angle from steep angled cone (interior angle > 90 degrees) to a shallow angle cone (interior angle < 90 degrees) has the effect of broadening out the wave length. This increases the effective band RPM band width of the pipe since there greater flexibility of crank angle for which an appropriate pressure will at the exhaust port. This also has the effect of decreasing the maximum attainable volumetric efficiency of the pipe since the peak pressure amplitude is diminished by spreading out the waves energy over a longer wavelength. Note that if the diameter of section L1 and the belly section are kept constant, changing the angle and changing the length of the diverging/converging section is geometrically the same.
- The ratio of the cross section of section L1 and the belly section - the ratio is largely dependent on the desired angle and length of the diverging/converging sections and the minimum diameter desired to avoid impeding the flow of the exhaust gases.
Further Investigation
[edit | edit source]For further investigate of the operation of two-stroke engines with tuned exhaust pipes it is most appropriate to analyze actual test data. For this we can go to the TFX website where they demonstrate their testing and data analysis software, or read the paper referenced below titled "Exhaust Gas Flow Behavior in a Two-Stroke Engine.
For the class presentation I would like to do both given sufficient time.
References
[edit | edit source]- Exhaust Gas Flow Behavior in a Two-Stroke Engine; Y. Ikeda T. Takahashi, T. Ito, T. Nakajima; Kobe Univ.; SAE 1993
- Power Tuning - Two Stroke Engines
- 2 STROKE WIZARD - Tuned Pipe Design Software
- Ian Williams Tuning MOTA Tune Pipe Design Software
- Les phénomènes d'ondes dans les moteurs; M. Borel; Edition TECHNIP; 2000
- Engineering Acoustics Course Notes; McGill University MECH 500; L. Mongeau; 2008
- Engineering Acoustics; L. Kinsler, A. Frey; 4th Edition; 2000